MOTOR APPLICATIONS
PROVIDING SOLUTIONS FOR POWER UTILIZATION EQUIPMENT AND MOTOR APPLICATIONS, INCLUDING ELECTRIC MOTORS SINCE 1951.
Their motor location and application typically identify the insulation components used in these electric motors. The Gund Company offers a variety of insulation component solutions for various crucial areas of electric motors:
- Rotors: The rotor is the moving component of the electromagnetic system in the electric motor. Its rotation is due to the interaction between the stator windings and the magnetic fields, which produce torque around the rotor’s axis and mechanical power to the shaft.
- Stators: The stator is the stationary part of a rotary system and utilizes the incoming power to apply electromotive forces to move the rotor. Making it an essential part of electric motors.
ELECTRIC MOTOR INSULATION MATERIALS
Insulation components for electric motors must be precisely measured, machined, and installed.
The Gund Company employs expert staff to run our state-of-the-art fabrication equipment. Coupled with our rigorous Quality Assurance program and in-process inspections, The Gund Company can offer our customers high-quality products that meet the electric motor market’s challenging application demands.
AC MOTOR STATOR INSULATION:
- Topsticks
- Wedges
- Filler Strips
- Phase Separators
- Slot Liners
- Tapes
- Tie Cord
- Lead Wire Insulation
- Terminal Boards
- Lead Clamps
- End Winding Support Rings
- End Winding Support Blocks
- Felt
- End Baffles
AC MOTOR ROTOR INSULATION:
- Topsticks
- Wedges
- Pole Collars
- Slot Liners
- Turn-to-Turn Insulation
- Pole Blocking
- Lead Clamps
DC STATOR INSULATION:
- Pole Collars
- Turn-to-Turn Insulation
- Lead Clamps
- Blocking
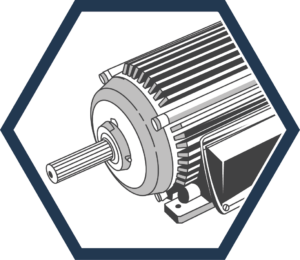
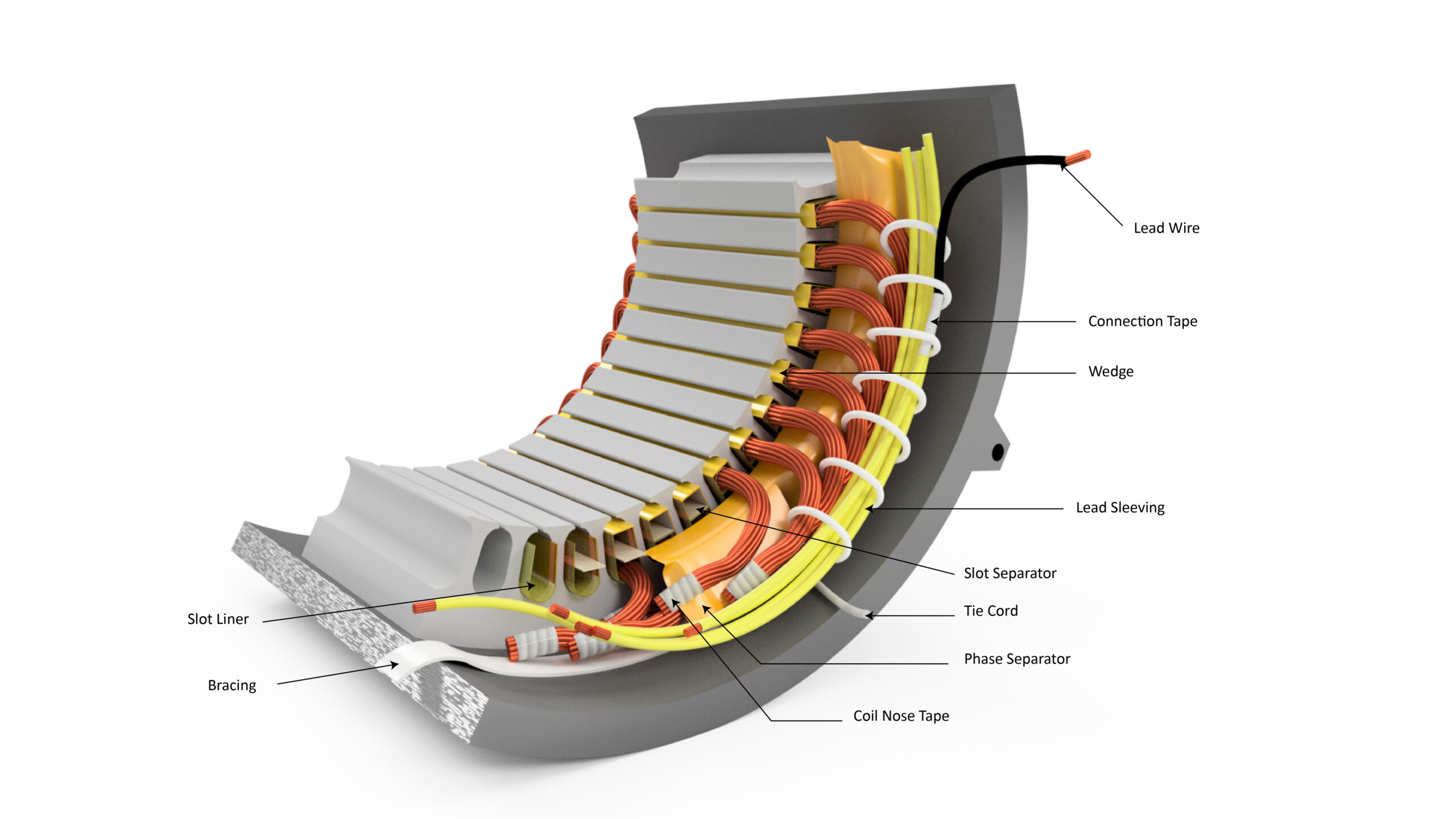
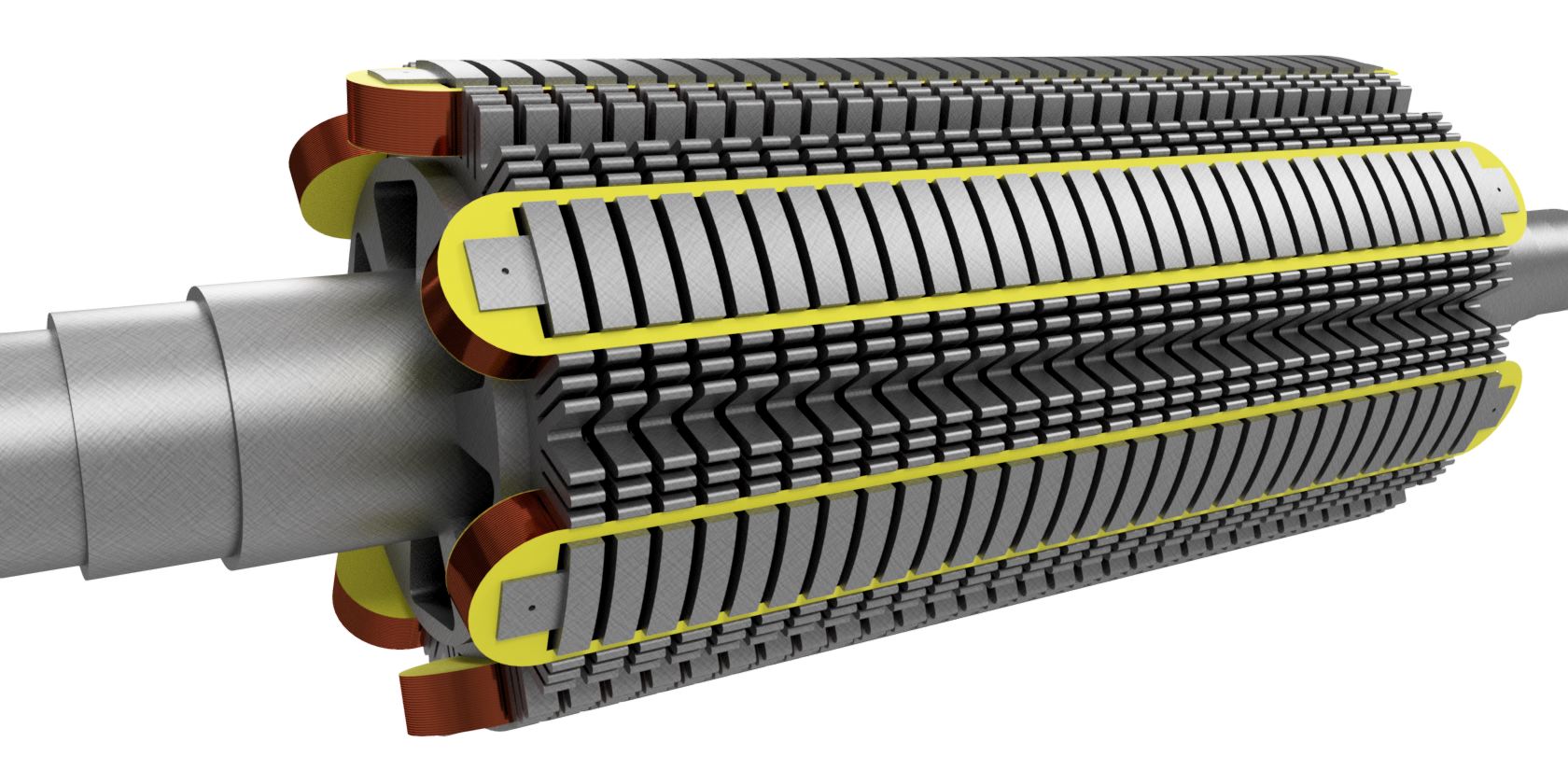
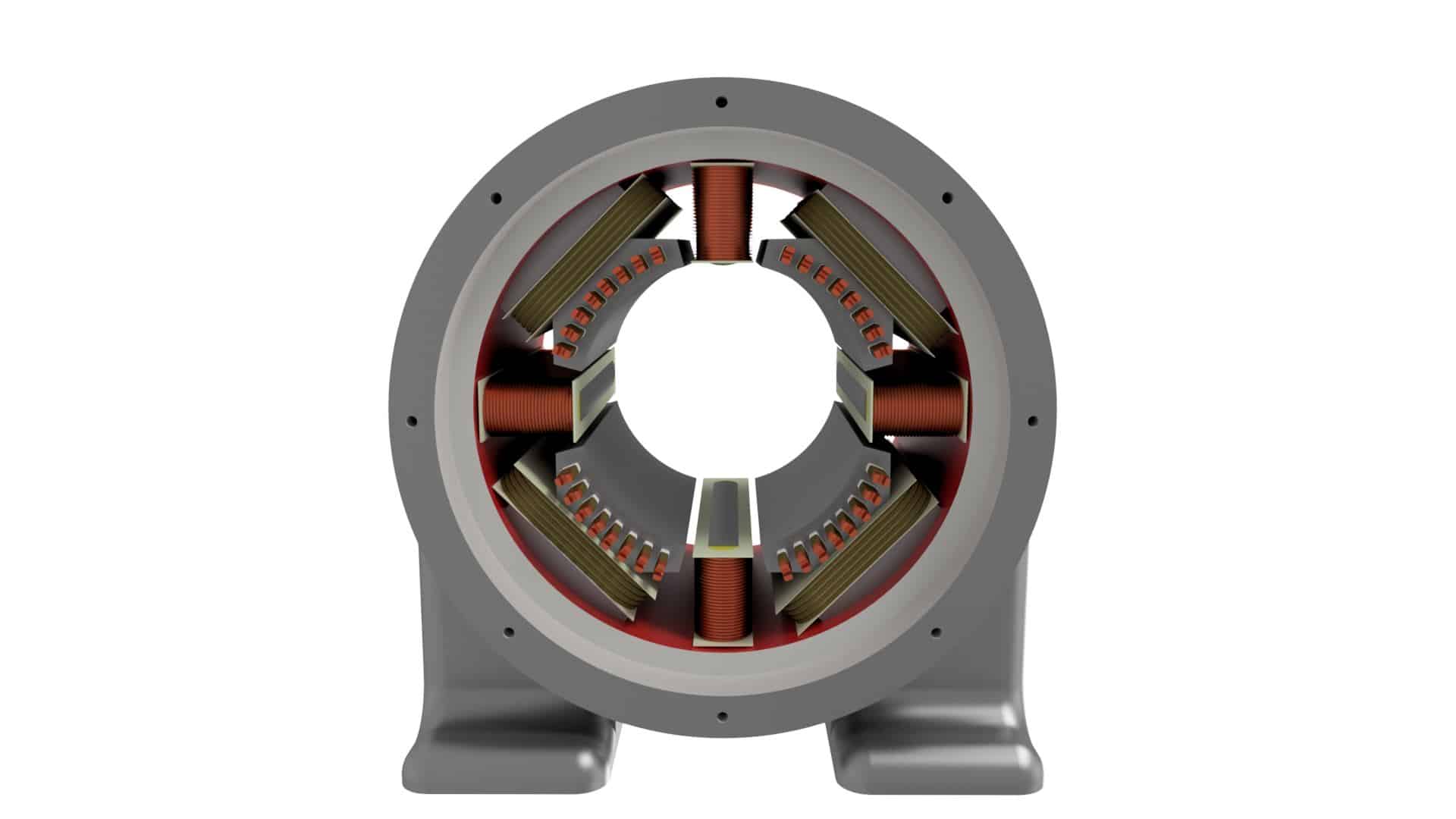
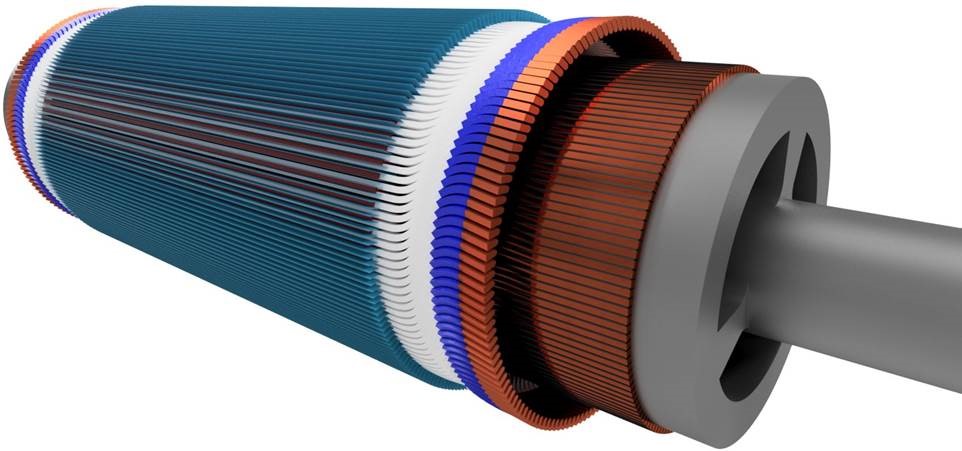
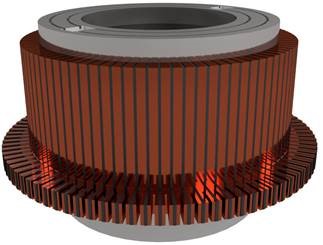
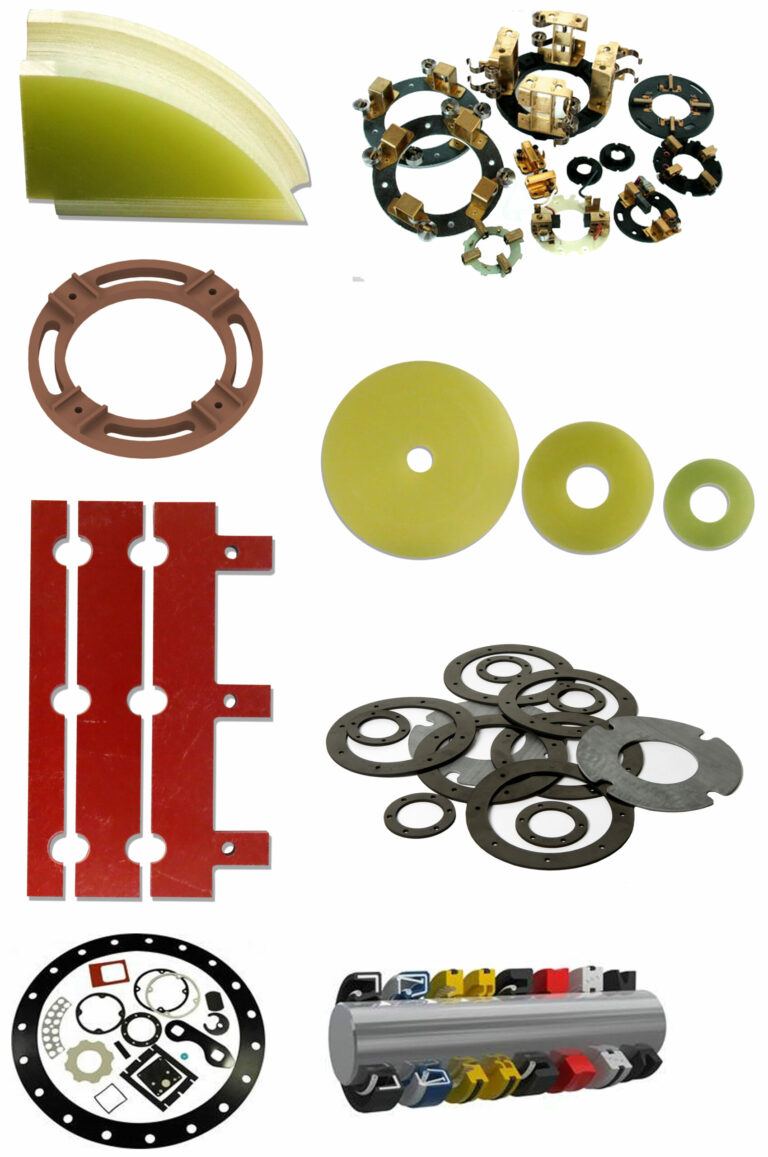
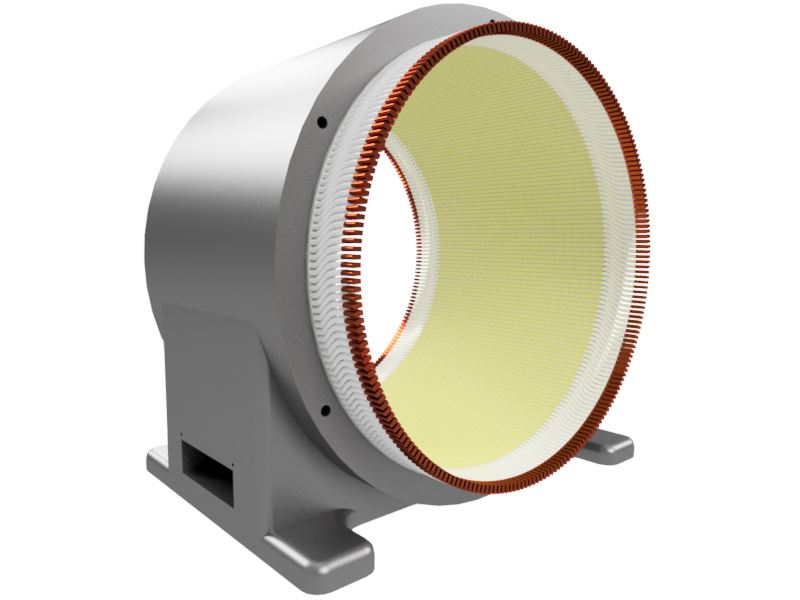
DC ARMATURE INSULATION:
COMMUTATORS:
- Mica HD
- Mica V-Rings
- Binding Tape
OTHER MOTOR INSULATION COMPONENTS:
- Elastomeric Gaskets
- Terminal Box Gaskets
- Enclosure Gaskets
- O-Rings
- Riser Trays
- Convolute Lead Trays
- Washer and Bushings
- Shaft Seals
- Threaded Rod
- Insulated Tubing
Our custom-fabricated parts adhere to ISO 9001:2015 certified quality systems, ensuring superior quality and precision. We employ a consultative engineering approach, collaborating closely with our customers to identify the optimal material choices for AC and DC electric motor applications. This process consistently produces engineered components that not only meet but also exceed the rigorous mechanical and electrical criteria of the application and major OEMs.
Simply provide your part’s operating parameters, function, and operating environment, and we will help you determine the best material options for your application. The Gund Company also offers various specialty materials used in electric motor insulation applications, including magnetic laminates, semi-conductive laminates, flexible laminates, and tapes. Contact one of our electric motor material specialists to review your application and material requirements. The Gund Company is pleased to offer five samples, of your choice, of our most popular materials that interest
Common Rigid Insulation Materials in Motors | |||
---|---|---|---|
![]() | |||
Mica M | G-3, PFGC 201 | G-9, MFGC 201 | |
Mica HD | G-11, EPGC 203 | GPO-3, UPGM 203 | |
G-10, EPGC 201 | Class F GPO-1, UPGM 201 | Class H GPO-1, UPGM 201 | |
C, CE, LE, PFCC 201/202/204 | N155 | N180 | |
Class R GPO-1, UPGM 201 | H755 | EMD Grades | |
Top Ripple Spring | T160 | N220 | |
Side Ripple Spring | FR4, EPGC 202 | SG200 | |
Semi-Conductive Laminate: C109 | MagNohl® | HST II | |
PCGP-HT | |||
Click here to view additional material datasheets. |
Common Flexible Insulation Materials in Motors | ||
---|---|---|
![]() | ||
Dacron/Mylar/Dacron (DMD) | Polyester PET Film | |
Rag/Mylar, Rag/Mylar/Rag (RMR) | Nomex/Mylar/Nomex (NMN) | |
Nomex® Meta-Aramid Papers | Epoxy Coated Nomex® | |
G-Flex™ Meta-Aramid Papers | Vulcanized Fibre | |
Kapton tape | PTFE Tape | |
Click here to view additional material datasheets. |
Common Elastomeric Materials in Motors | ||
---|---|---|
![]() | ||
Neoprene | Cork-Rubber | |
Nitrile | EPDM | |
Silicone | FKM (Viton®) | |
Butyl | Sponge | |
Click here to view additional material datasheets. |
The Gund Company also offers a wide variety of elastomeric materials for all your O-ring and gasket needs.