Thermoset Rigid Composite Material Solutions
THERMOSET COMPOSITE MATERIALS MANUFACTURER & FABRICATOR
THE GUND COMPANY FOCUSES ON TWO MAIN TYPES OF THERMOSET RIGID COMPOSITE MATERIALS, HIGH-PRESSURE LAMINATES, AND LOW-PRESSURE LAMINATES.
Thermoset rigid laminates are composite materials. By definition, composite materials consist of two or more materials. In most thermoset rigid laminates, the primary materials include a substrate or base material such as paper, cotton cloth, or glass cloth, along with a resin or adhesive such as epoxy, melamine, or silicone. For thermoset laminate production, the base material is coated with an adhesive so that layers of material can be pressed into sheet form under heat and pressure.
Thermosetting materials are strong materials consisting of resin and a substrate. They do not melt at high temperatures and cannot be reformed. They are rigid by nature, so they are easily machinable. Due to the use of these materials in electrical equipment, the National Electric Manufacturers Association (NEMA) has established industry standards for the minimum test values by property for each material. Thermoset materials are commonly referenced using the NEMA grade designation.
The Gund Company focuses on two main types of thermoset rigid composite materials, high-pressure laminates, and low-pressure laminates.
We are also one of North America’s largest filament wound-tube and pultrusion manufacturers, with competence in multiple facilities. In addition, we can supply compression and resin transfer molded parts, convoluted wound tubes, autoclaves, and large layup and spray products. We have the resources and capabilities to manufacture products and processes rapidly.
Types of Thermoset Rigid Composite Products:
- High-Pressure Laminates
- Filament & Convolute Wound Tubing
- Low-Pressure Laminates
- Pultruded Shapes (Rod, Tube, Angle, & Channel)
- Compression Molded BMC
- Vacuum Infusion Molding
- Autoclave Composite Molding
Typical Product Names:
- Glass Epoxy, NEMA Grades FR4, G-10, G-11
- Glass Silicone, NEMA Grade G-7
- Silicone Bonded Mica Paper Laminate
- Filament Wound Glass Epoxy Tubing
- Glass Polyester, NEMA Grade GPO-3
- Stand-Off Insulators
- Custom Composite Molded Components
HIGH-PRESSURE LAMINATES
HIGH-PRESSURE LAMINATES MAY USE SEVERAL SUBSTRATES SUCH AS KRAFT PAPER, MICA PAPER, CANVAS, LINEN (COTTON) CLOTH, OR GLASS CLOTH.
Typical resins used in a high-pressure laminate manufacturing process include phenolic, epoxy, melamine, silicone, and polyimide. The process produces outstanding mechanical strength, especially in compression. High-pressure laminates also have excellent dielectric strength and electrical properties. Each combination of substrate and resin provides a different set of properties.
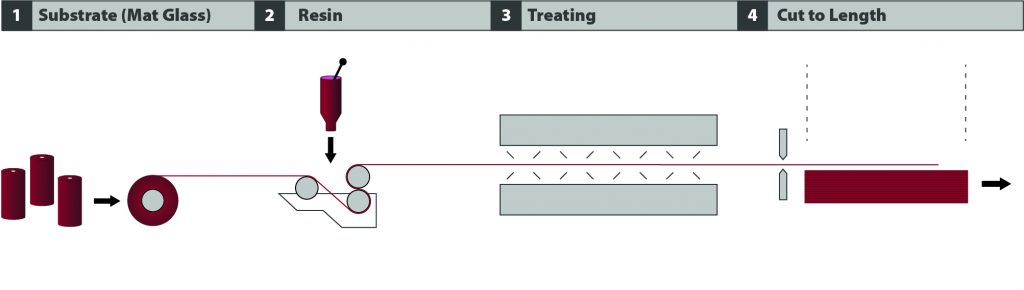
The manufacturing process for our high-pressure thermoset laminate sheet material begins with selecting the proper substrate and resin for the particular application. All high-pressure thermoset laminates follow the same basic approach as follows:
- Step 1) Substrate or base materials such as paper or glass cloth arrive at the plant in master rolls with a thickness ranging from .003″ to .010″.
- Step 2) The base material is passed through a resin bath to impregnate the substrate with a resin such as phenolic, epoxy, melamine, or silicone.
- Step 3) After the base material has been impregnated, it is passed through a treating oven to drive off the resin’s solvents and precisely allocate the correct amount of resin on the substrate.
- Step 4) After being treated, the composite is now considered in its “B-Stage.” The B-Stage composite is then cut to size and stacked (called Prebuild), depending on the sheet’s thickness. The material is then loaded into the laminating press.

- Step 5) The cut-to-size prebuild is placed in the press under heat and pressure, which results in the finished laminate sheets. Typical press loads can hold anywhere from 8″–14″ worth of sheet material and may take up to several hours to fully cure, depending on the grade being produced.
- Step 6) After being removed from the press, the sheets are trimmed and sanded to thickness as required.
- Step 7) The sheets are inspected for quality, with many samples tested in the laboratory for specification compliance. Sheets are then packaged and shipped to one of our facilities for fabrication into machined components according to customer drawings and specifications.
High-pressure laminate is a longer process cycle than the low-pressure laminate manufacturing process, but it yields a higher mechanical strength. Unique properties produced by the high-pressure laminate manufacturing process allow for specific performance characteristics required by many demanding applications.
Check our Material Data Sheets Page to learn more about our high-pressure laminate materials.
LOW-PRESSURE LAMINATES
LOW-PRESSURE LAMINATES TYPICALLY USE A GLASS MAT SUBSTRATE. TYPICAL RESINS USED IN THE LOW-PRESSURE LAMINATE MANUFACTURING PROCESS INCLUDE POLYESTER, VINYL ESTER, AND EPOXY.
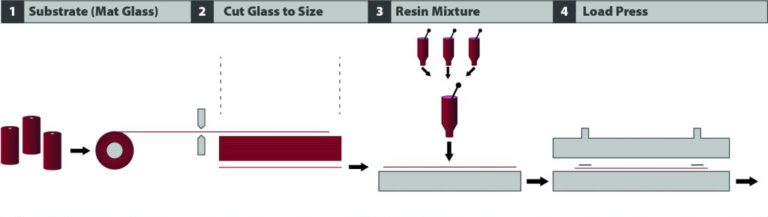
The process produces an excellent combination of mechanical strength, dielectric properties, and thermal performance. One advantage of the low-pressure laminate manufacturing process is using various fillers and additives to create a range of desirable properties, from flame-retardance to resistance-tracking.
The manufacturing process for our low-pressure thermoset laminate sheet materials begins with selecting the proper resin formulation to provide the properties required for a specific application. Low-pressure laminates are typically made following the same basic steps as follows:
- Step 1) Continuous strand random mat glass is received in roll form with various weights, constructions, sizing, and thicknesses depending on the manufactured product.
- Step 2) Glass mat is cut to length to create glass packages of various builds depending on the sheet thickness and product formulation for the product being manufactured.
- Step 3) Resins are received and stored in large tanks. Depending on the material grade, there may be as many as 20 resin system components.
- Step 4) The various resin components are mixed with filler additives to add properties such as track resistance, flame- retardance, and thermal endurance. The resin is then applied to the glass fiber package on an automated press loading table with CNC-controlled weight scales.
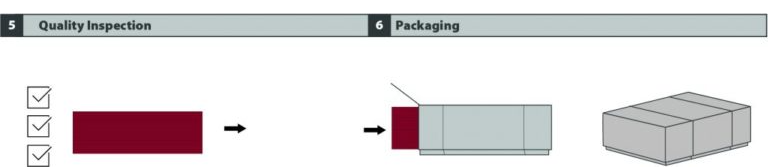
- Step 5) The press is automatically loaded and computer-controlled for the proper pressure and heat-curing profile for the product being manufactured. The sheets are molded individually in a press cycle that can vary from several minutes to a half-hour.
- Step 6) Sheets are unloaded with automated material handling equipment. Sheets are inspected for quality and manufacturing tolerances, with sample lots sent to the laboratory for verification testing for properties, including flexural strength and dielectric strength.
- Step 7) Sheets are labeled by lot and packaged for shipment to our fabrication plant for machining into finished parts per our customer requirements.
The low-pressure laminate manufacturing process is considered more cost-effective than the high-pressure laminate process due to the faster cycle time from the process’s beginning to the end. With composite materials, there are always trade-offs among the various materials’ properties depending, in part, on the manufacturing process.
Check our Material Data Sheets Page to learn more about our low-pressure laminate materials.