GENERATOR MATERIAL SOLUTIONS
THE GUND COMPANY IS A MANUFACTURER AND FABRICATOR OF ENGINEERED INSULATION MATERIAL SOLUTIONS FOR POWER GENERATION EQUIPMENT, INCLUDING STEAM, HYDRO, AND WIND GENERATORS.
In generators, the insulation material components are specific to their application and location within the generator. Standard generator components are:
- Rotor Field:
The rotor is the moving component of the generator that provides the magnetic field. Its rotation is provided by the prime mover (turbine, water, the wind, motor, engine, and more).
- Stators:
The stator is the stationary part of a generator system. The stator provides power output and keeps the magnetic field (rotor) aligned.
- Exciters:
In general terms, the generator rotor is a rotating electromagnet that requires direct current (DC) to excite the magnetic field. The exciter produces this DC voltage.
- Accessories and Auxiliary Components:
Many generator accessories and auxiliaries require insulation components designed to be a perfect fit. They also require specialty (auxiliary) tools, such as rotor stands, rotor coupling shoes, and temporary blocking to install the generator insulation components.
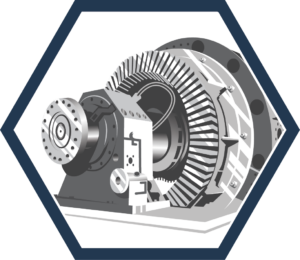
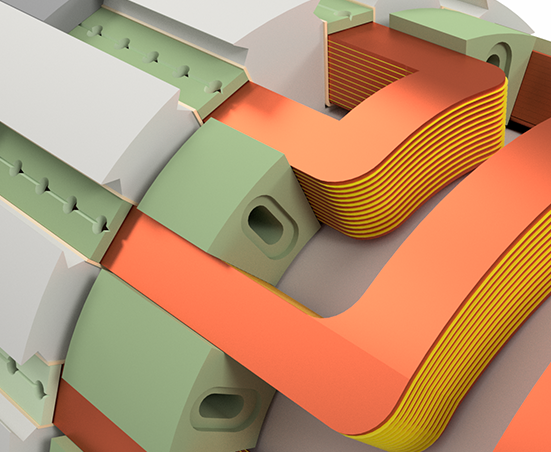
TURBINE GENERATORS
FOR A TURBINE GENERATOR, SPINNING A 50+ TON ROTOR AT 3,600 RPMS CREATES WELL OVER 5GS OF CENTRIFUGAL FORCE ON THE GENERATOR ROTOR'S INSULATING COMPONENTS.
When it comes to material selection options and fabrication precision, The Gund Company has decades of experience assisting customers in making insulation application engineering decisions for their generators. We supply complete generator rotor insulation kits with all insulating components for a rewind. Equally important are the stator insulation components. A tight stator wedge system minimizes wear, vibration, and abrasion and supports proper generator operation.
Outage duration is a critical aspect of cost and profitability in the power generator market space. Our outage management process covers everything from material selection reviews to reverse engineering components to project review meetings and logistics management for timely and expedited deliveries to the site or service provider. The Gund Company employs an expert staff to run our state-of-the-art fabrication equipment. Coupled with our rigorous Quality Assurance program and “in-process” inspections, The Gund Company provides our customers with high-quality insulation and elastomeric products that meet the generator market’s challenging applications. Contact a generator material specialist today to request a copy of our generator repair project checklist or schedule a lunch-and-learn event at your facility.
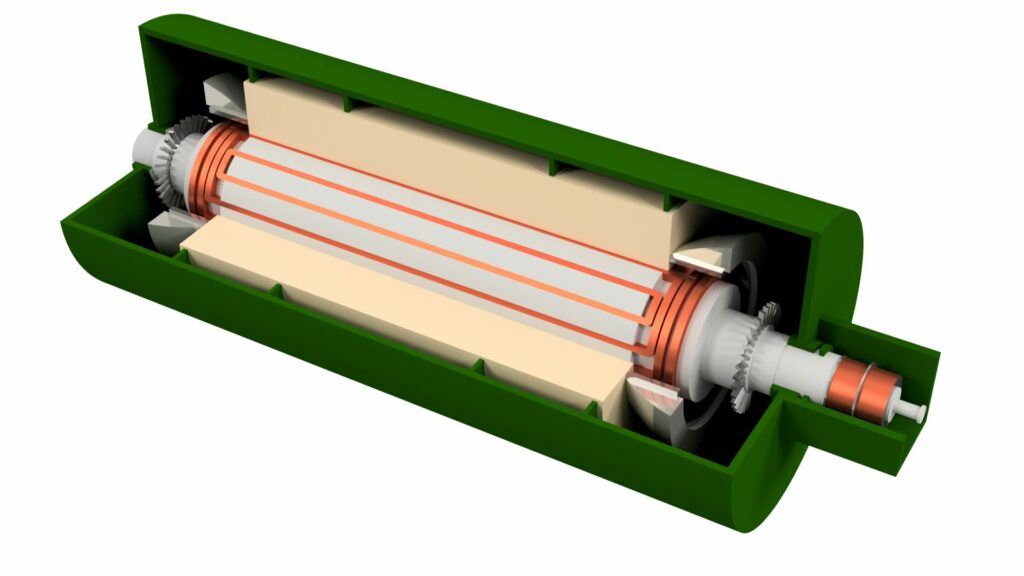
TURBINE GENERATOR ROTOR INSULATION:
- Vented and Non-Vented Turn Insulation
- Turn-to-Turn Insulation
- Compound Ventilated & Standard Creepage Blocks
- Slot Cells/Liner/Armor: Us, Ls, Steps, & Clubfoot
- Sub-Slot Insulation
- Bore Copper Insulation
- Radial & Axial Blocking
- Temp Blocking
- Retaining Ring Insulation
- Rotor Shoes
- Bearing & Oil Seal Deflector Insulation
- Exciter Insulation
- Creepage Block
- Sub-slot Cover
- Cover Channels
- Retaining Rings (steel)
- Collector Rings (steel)
- Collector Assemblies
- Collector Housing Covers (composite or steel)
- Bearing Shoes (composite and/or wood)
- Coil Blocking, Permanent Blocking, Distance Blocking
- Ring Insulation
- Axial Lead Tubes, Bore Tubes
- Temporary Wood
- Main Lead & Collector Insulation
- Retaining Ring Insulation (Formed, molded, and single-piece available)
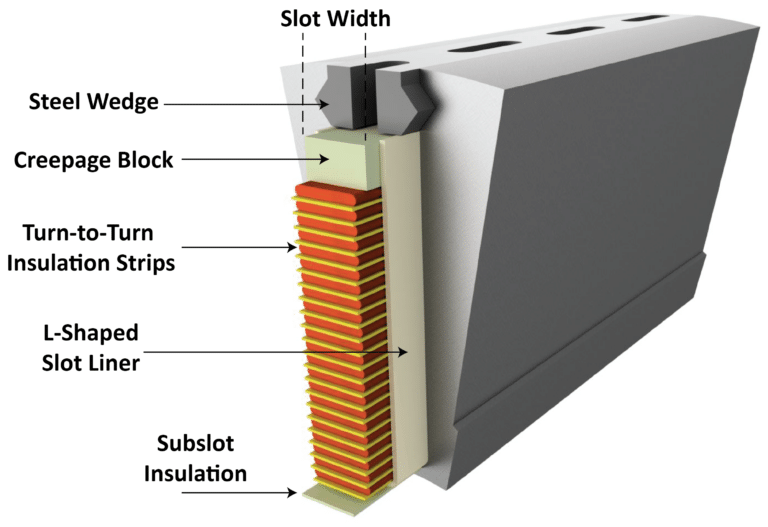
Common Rotor Materials & Their Applications | ||
---|---|---|
Description | Material | Application |
130°C Glass Epoxy | NEMA G-10, IEC EPGC 201 | Rotor Blocking, Subslot Insulation, Creepage Blocking |
155°C Glass Epoxy | NEMA G-11, IEC EPGC 203 | Rotor Blocking, Subslot Insulation, Creepage Blocking |
180°C Glass Epoxy | NEMA G-12 (G-11H), IEC EPGC 308 | Rotor Blocking, Subslot Insulation, Creepage Blocking |
Formable 155°C Glass Epoxy | NEMA G-11 (Formable), IEC EPGC 203 | Retaining Ring Insulation |
Teflon Coated 155°C Glass Epoxy | NEMA G-11 (PTFE Coated) | Retaining Ring Insulation |
Teflon Coated 180°C Glass Epoxy | NEMA G-12 (G-11H), PTFE Coated | Retaining Ring Insulation |
155°C Glass Polyester | NEMA GPO-1, IEC UPGM 201 | Rotor Blocking |
Enhanced 155°C Glass Polyester | IEC UPGM 205 | Rotor Blocking |
Turn Insulation | RotoGuard EG | Turn-to-Turn Insulation |
Turn Insulation | RotoGuard TIB | Turn-to-Turn Insulation |
Slot Liner | RotoGuard Slot Liner | Rotor Slot Insulation |
Turn Insulation | Epoxy Coated Nomex | Turn-to-Turn Insulation |
TURBINE GENERATOR ROTOR COPPER COMPONENTS:
- Insulated Collector Studs
- Main Lead Studs
- Collector Bars
- Hydrogen Bolt Seals
- Bore Seal Plates
- Flex Leads
- Coil Connectors
TURBINE GENERATOR ROTOR METAL COMPONENTS:
- Retaining Ring steel
- Collector Rings steel
- Rotor Wedge steel

TURBINE GENERATOR STATOR INSULATION:
- Wedges
- Semi-Conductive Fillers & Ripple Springs
- Sliders
- Top, Center, Bottom Filler
- Side Packing
- Surge Rings
- Spacer Blocks
- Basket Rings / Binding Bands
- Washers
- Baffles
- Gaskets
- Seals & O-Rings
- Support Ring, Binding Bands
- Z-Ring
- Nose Ring
- Hydrogen Seal Insulation
- Drive Boards
- Temp Slot Boards
- Coil Spacers
- Axial Supports/Gunstocks
- Liquid plumbing (copper)
- Brazed Plumbing/Fitting assemblies (steel and copper)
- End Winging Support (both Basket Assemblies and Cones)
- L-Bracket Supports
- Air Guides, Fan Nozzles, Blower Shrouds, and Gas Shields (Composite)
- Mica Tapes and Series Loop Insulation kits
Common Stator Materials & Their Applications | ||
---|---|---|
Description | Material | Application |
130°C Glass Epoxy | NEMA G-10, IEC EPGC 201 | Wedges, Slot Filler |
155°C Glass Epoxy | NEMA G-11, IEC EPGC 203 | Wedges, Slot Filler |
180°C Glass Epoxy | G-12 (G-11H), IEC EPGC 308 | Wedges, Slot Filler |
130°C Canvas Phenolic | LSBC | Wedges |
130°C Canvas Phenolic | PBBC | Wedges |
155°C Glass Polyester | IEC UPGM 205 | Wedges, Slot Filler |
Semiconductive Glass Polyester | C109 | Slot Filler |
Semiconductive Glass Epoxy | C209 | Slot Filler |
Semiconductive Side Packing | Side Ripple | Slot Filler |
Top Packing Material | Top Ripple Spring | Top Filler |
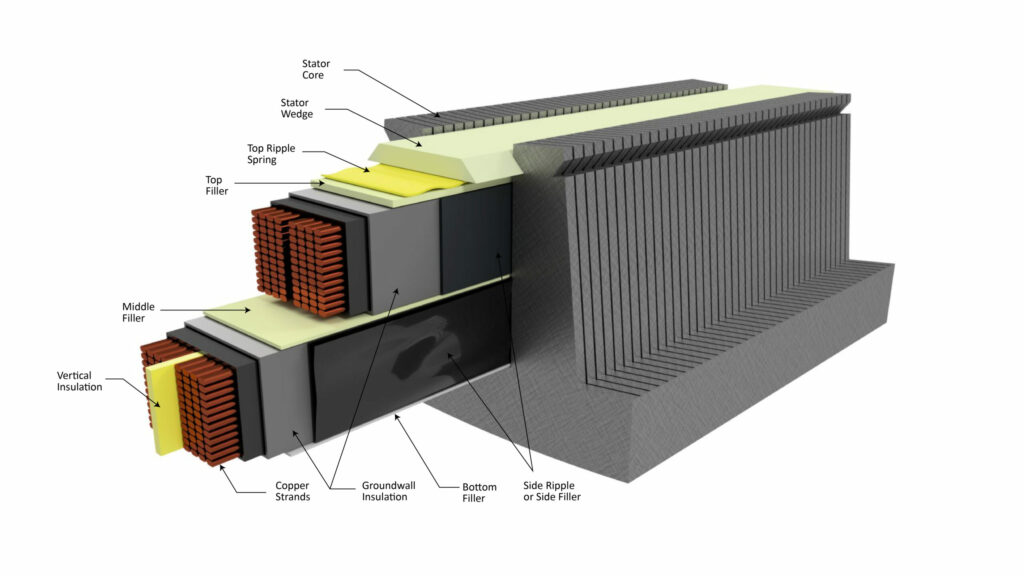
The Gund Company also offers a wide variety of elastomeric materials for all your O-ring and gasket needs.
HYDRO GENERATORS
THE GUND COMPANY CAN DELIVER THE RIGHT COMPONENTS TO THE PROPER SPECIFICATION, FROM REVERSE-ENGINEERED COMPONENTS TO PARTS FABRICATED FROM DRAWINGS, WHILE MEETING YOUR CRITICAL DELIVERY SCHEDULE.
We fabricate all types of stator wedges, including flat, tapered, measurement, and end wedges. We provide semi-conductive side fillers, side and top ripple springs, and center and bottom fillers. Our knowledge of materials and years of application experience allow us to serve the hydro-generator industry with unparalleled service.
HYDRO GENERATOR STATOR INSULATION:
- Wedges
- Fillers
- Ripple Springs
- End Caps
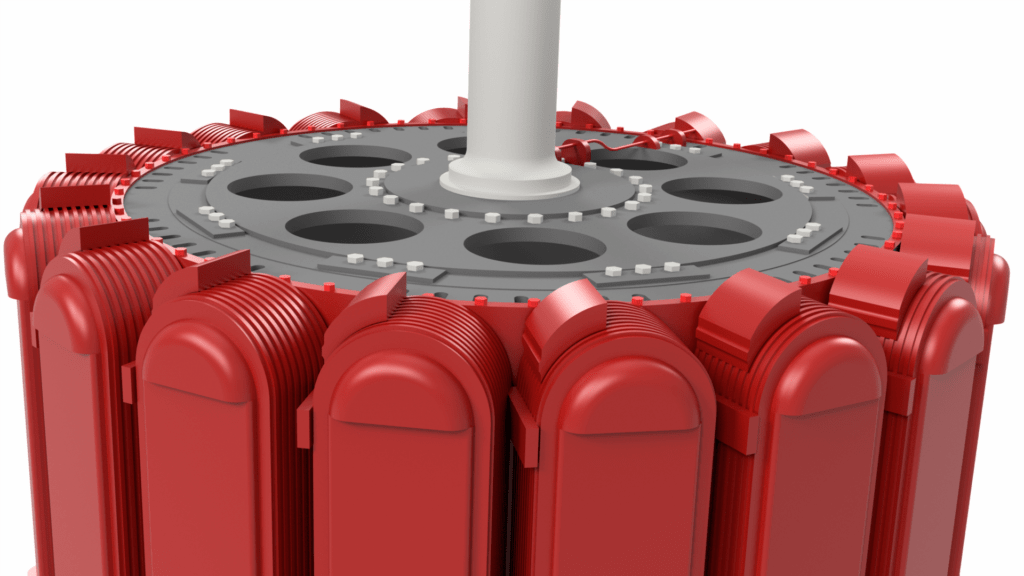
HYDRO GENERATOR ROTOR INSULATION:
- Rotor Pole Collars (Radius, Dished, Oversized)
- V-Blocks
- Rotor Pole Turn Insulation
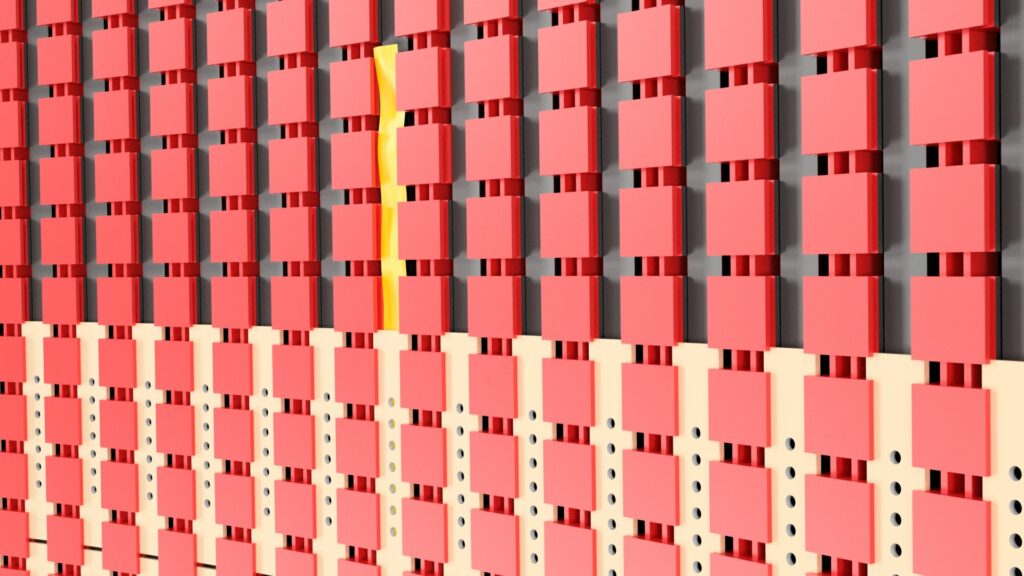
Hydro Generator Insulation Materials | ||
---|---|---|
Description | Material | Application |
130°C Glass Epoxy | NEMA G-10, IEC EPGC 201 | Pole Collars, V-Blocks |
155°C Glass Epoxy | NEMA G-11, IEC EPGC 203 | Pole Collars, V-Blocks |
180°C Glass Epoxy | NEMA G-12 (G-11H), IEC EPGC 308 | Pole Collars, V-Blocks |
155°C Glass Polyester | NEMA GPO-1, IEC UPGM 201 | Pole Collars, V-Blocks |
Enhanced 155°C Glass Polyester | U205 (UPGM 205) | Pole Collars, V-Blocks |
Turn Insulation | RotoGuard TI/TIB | Turn-to-Turn Insulation |
130°C Glass Epoxy | NEMA G-10, IEC EPGC 201 | Wedges, Slot Filler |
155°C Glass Epoxy | NEMA G-11, IEC EPGC 203 | Wedges, Slot Filler |
180°C Glass Epoxy | NEMA G-12 (G-11H), IEC EPGC 308 | Wedges, Slot Filler |
130°C Canvas Phenolic | LSBC | Wedges |
130°C Canvas Phenolic | PBBC | Wedges |
155°C Glass Polyester | NEMA GPO-1, IEC UPGM 201 | Wedges, Slot Filler |
Enhanced 155°C Glass Polyester | U205 (UPGM 205) | Wedges, Slot Filler |
Semiconductive Glass Polyester | C109 | Slot Filler |
Semiconductive Glass Epoxy | C209 | Slot Filler |
Semiconductive Side Packing | Side Ripple | Slot Filler |
Top Packing Material | Top Ripple Spring | Top Filler |
The Gund Company also offers a wide variety of elastomeric materials for all your O-ring and gasket needs.
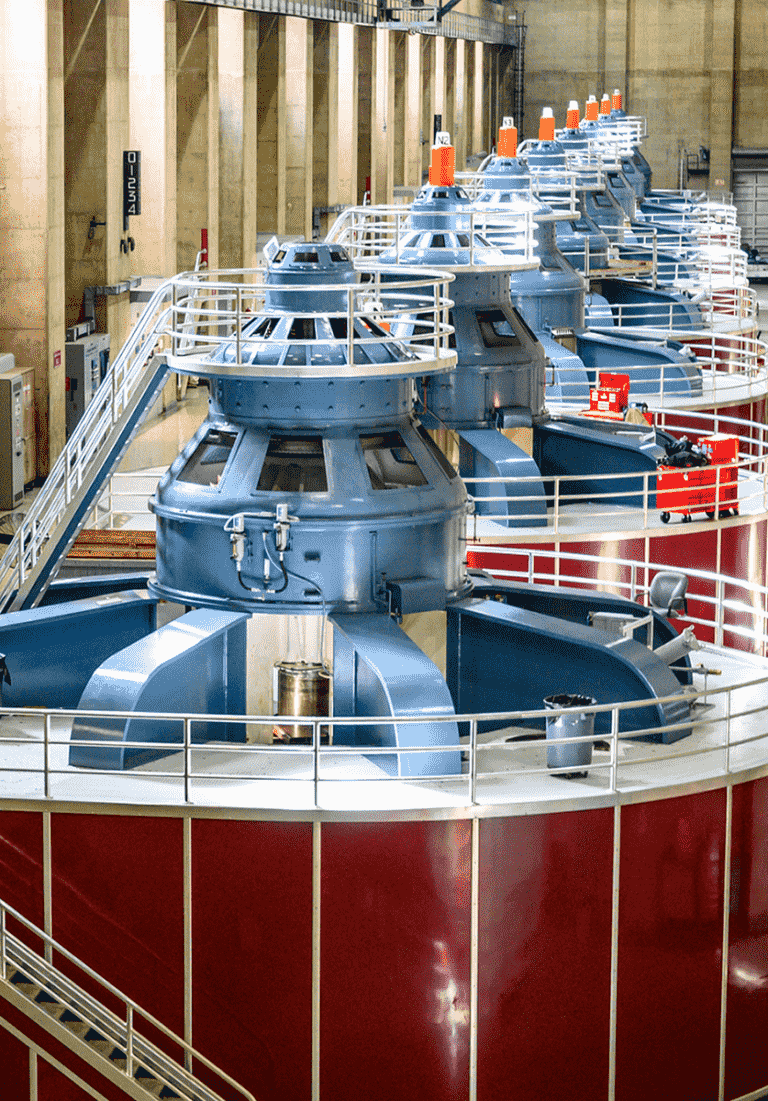
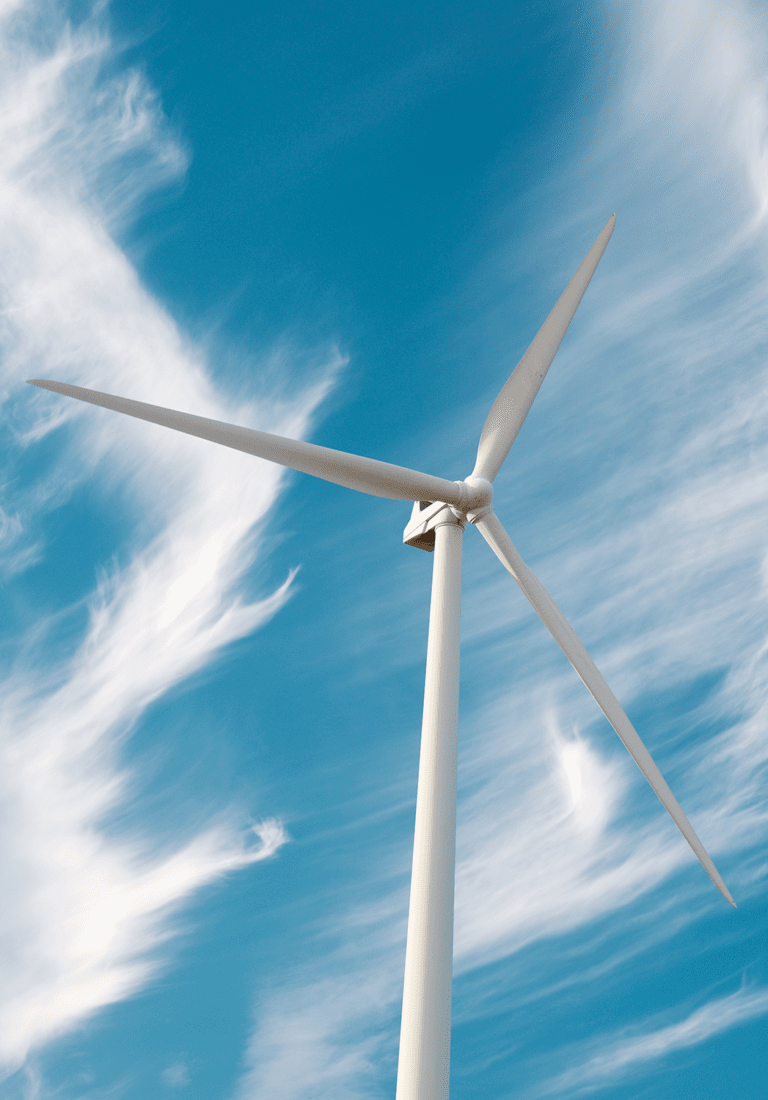
WIND GENERATORS
THE GUND COMPANY IS A MANUFACTURER AND FABRICATOR OF ENGINEERED MATERIAL SOLUTIONS FOR WIND GENERATORS.
We fabricate all types of stator wedges, including magnetic wedges. We provide semi-conductive side fillers, side and top ripple springs, and center and bottom fillers. Our knowledge of materials and years of application experience allow us to serve the wind generator industry with unparalleled service.
WIND GENERATOR INSULATION COMPONENTS:
- Magnetic & Non-Magnetic Wedges
- Magnetic & Non-Magnetic Topsticks
- Barriers
- Insulators
- Filler Strips
- Slit Coil Insulation
- Formed Slot Liners
- Flexible Papers & Films
"GEN SET" & SPECIALTY GENERATORS
THE GUND COMPANY IS A MANUFACTURER AND FABRICATOR OF ENGINEERED MATERIAL SOLUTIONS FOR GEN SETS AND SPECIALTY GENERATORS.
We fabricate all types of stator wedges, side fillers, and slot insulation. Our knowledge of materials and years of application experience allow us to serve the generator industry with unparalleled service.
- Wedges
- Fillers
- Top Sticks
- End Caps
- Barriers
- Insulators
- Gaskets
- O-Rings
- Washers
- Baffles
- Impregnated Roving
- PSA Tapes & Tie Cords
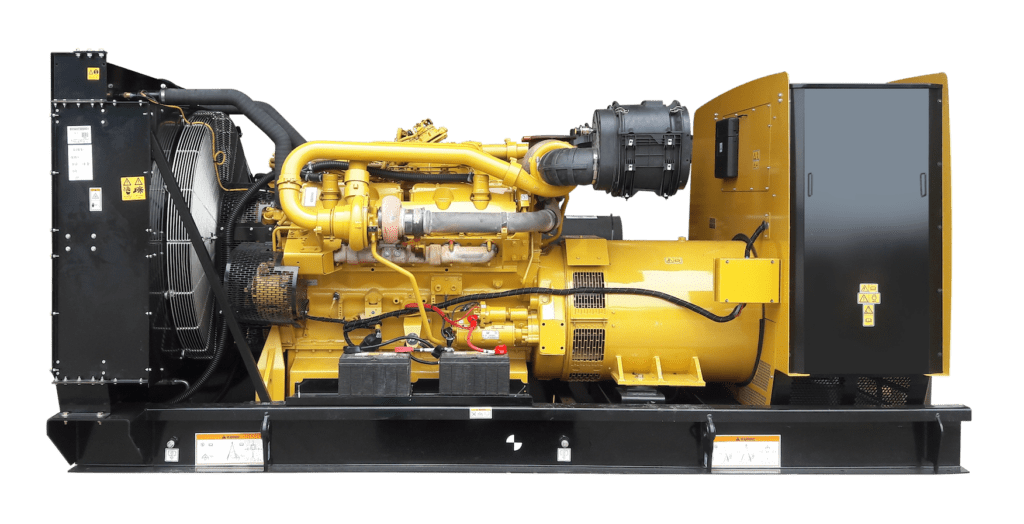
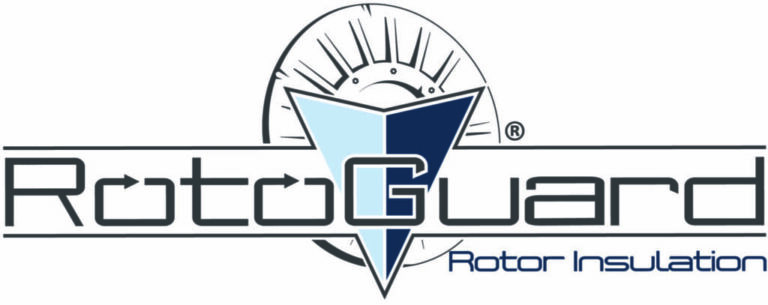
RotoGuard Insulation Protection Packages are a family of products that The Gund Company has developed to meet our customers’ specifications. Our aerospace manufacturing process enables us to provide high-quality slot liner and turn insulation that meets or exceeds OEM specifications. The result is a series of high-quality generator insulation products that save installation and schedule time. Visit our RotoGuard® Insulation Protection Page to Learn More.