Thermoplastic Material Solutions
THERMOPLASTIC MATERIALS
THERMOPLASTIC MATERIALS ARE MANUFACTURED FROM POLYMER RESINS. WITH APPLIED HEAT, THERMOPLASTICS LOSE THEIR RIGIDITY BECOMING MOLDABLE OR FORMABLE. WHEN COOLED, THE MATERIAL RETURNS TO ITS ORIGINAL STATE MAINTAINING ALL MECHANICAL, THERMAL, AND ELECTRICAL PROPERTIES. BECAUSE THIS PROCESS CAN BE REPEATED, THERMOPLASTIC PARTS ARE OFTEN RECYCLABLE AND CAN BE MANUFACTURED BY MANY DIFFERENT METHODS.
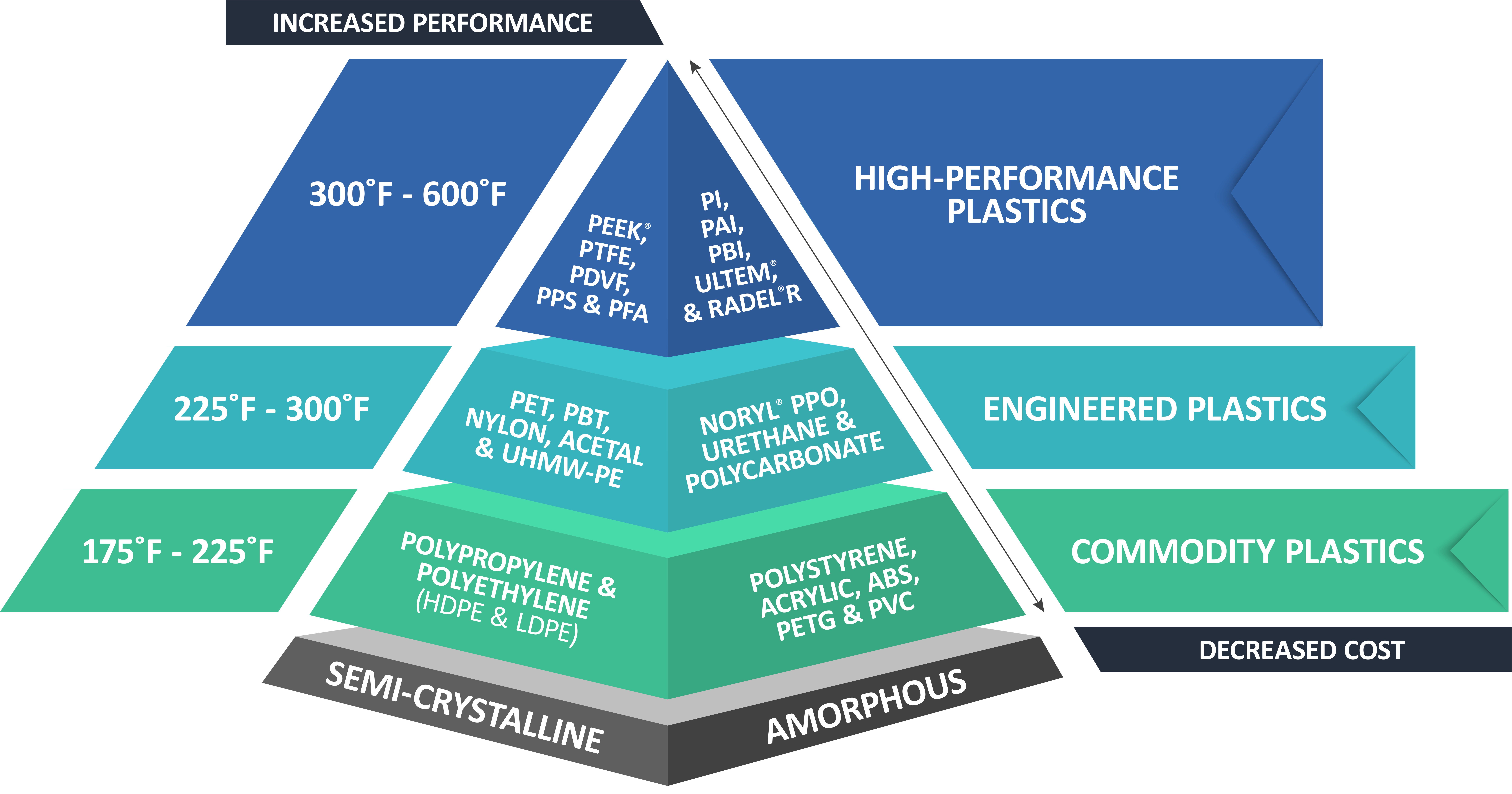
HIGH-PERFORMANCE THERMOPLASTICS
HIGH-PERFORMANCE PLASTICS MAY BE NECESSARY FOR THE MOST DEMANDING OR SPECIALIZED APPLICATIONS.
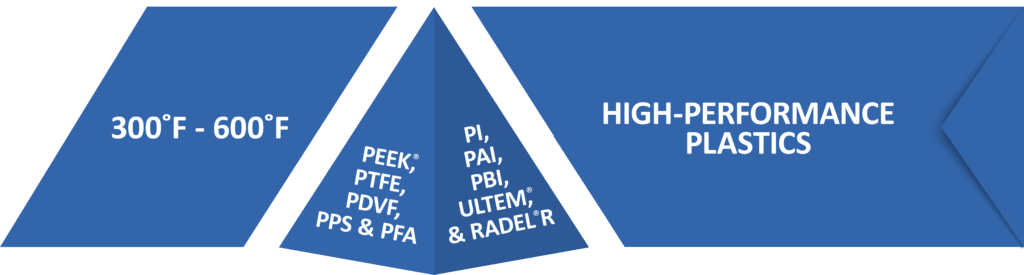
High-performance thermoplastics can withstand very high temperatures and offer excellent chemical resistance. These materials are often suited for aerospace applications but can also be used for thermal insulators, high-performance bearings, and electrical connectors in extreme environments. High-performance thermoplastics feature the highest temperature resistance and load-bearing capabilities, among other properties.
COMMON APPLICATIONS USING HIGH-PERFORMANCE THERMOPLASTICS
- Aerospace
- Oil & Gas
- Medical & Healthcare
- Food Service
- Electronics
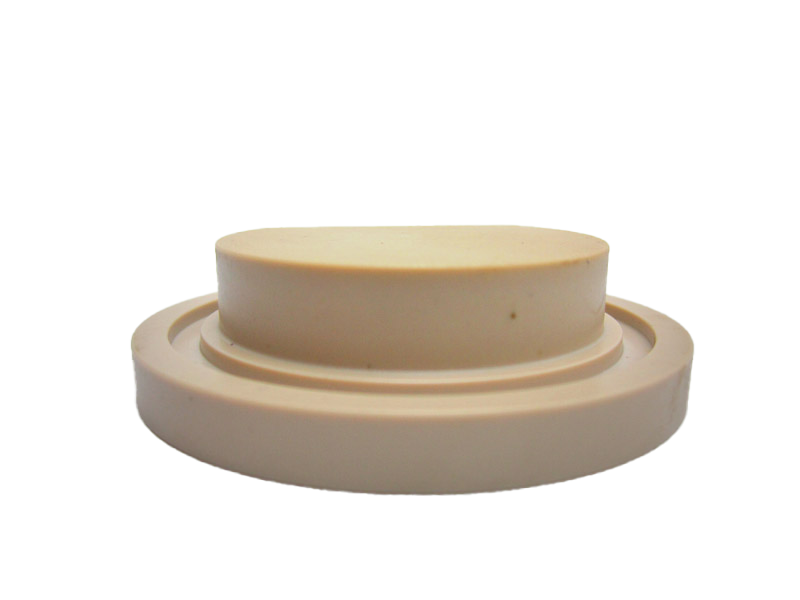
An alternative to metal, PEEK offers peak performance. PEEK is a lightweight and chemically inert material with superior strength properties used in extreme environments.
- Withstands Very High Temperatures
- Resistant to Aggressive Chemicals
- Superior Mechanical Properties
- Biocompatible
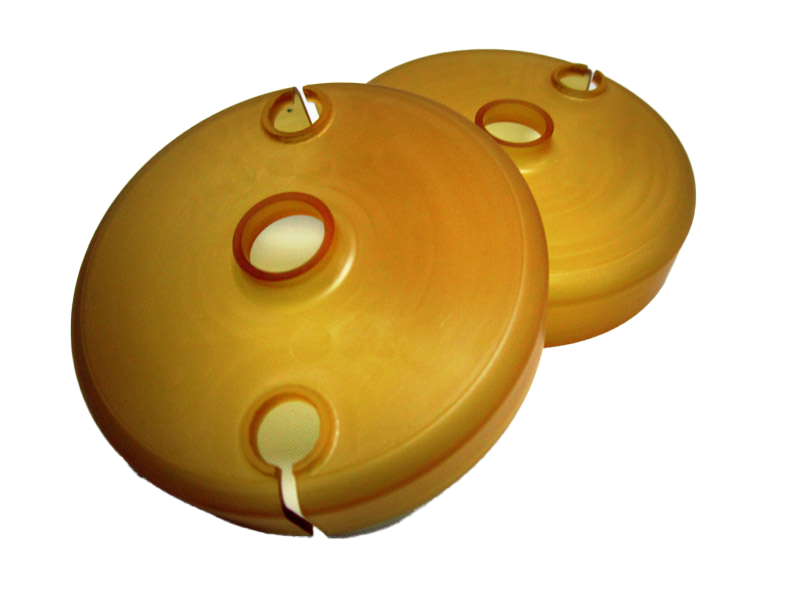
PEI offers exceptionally high impact and tensile strength. It exhibits excellent heat resistance and dielectric strength making it suitable for electrical applications.
- High Temperature Resistance
- Very High Dielectric Strength
- Great Dimensional Stability
- Easy to Process
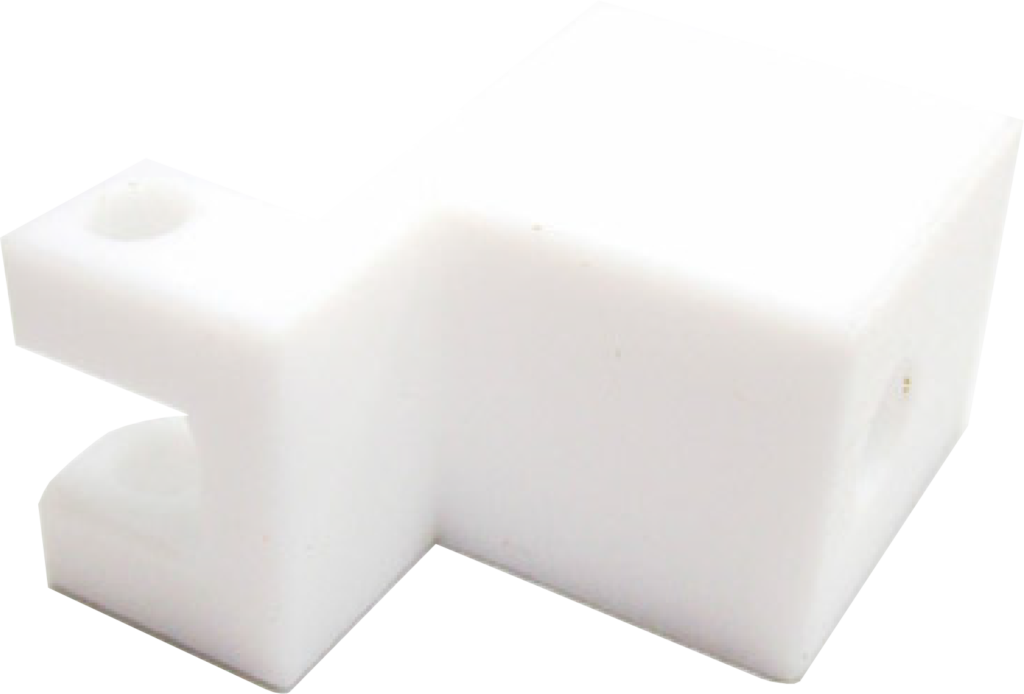
A hydrophobic material, PTFE offers exceptionally high dielectric strength at high temperatures. PTFE is corrosion-resistant and resistant to nearly all chemicals.
- Hydrophobic
- Low Surface Friction
- Chemically Inert
- Excellent Insulating Properties
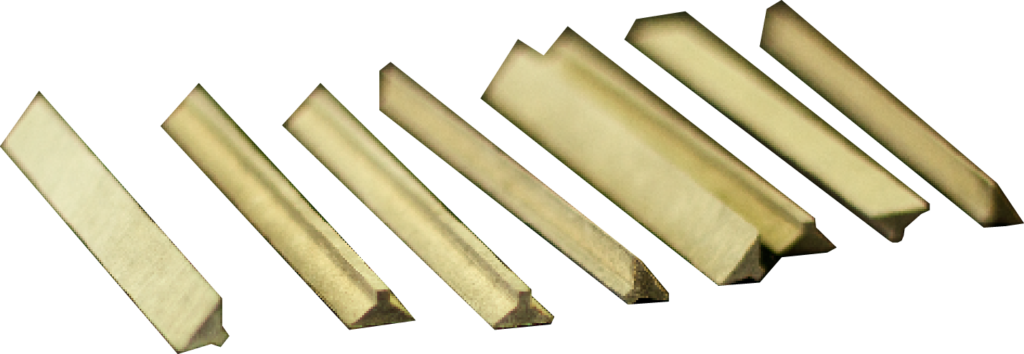
PPS is a naturally flame-resistant thermoplastic operating at extremely high temperatures. PPS exhibits high creep resistance and dimensional stability.
- Withstands Very High Temperatures
- Excellent Dimensionally Stability
- Flame-retardant
- Wear Resistant
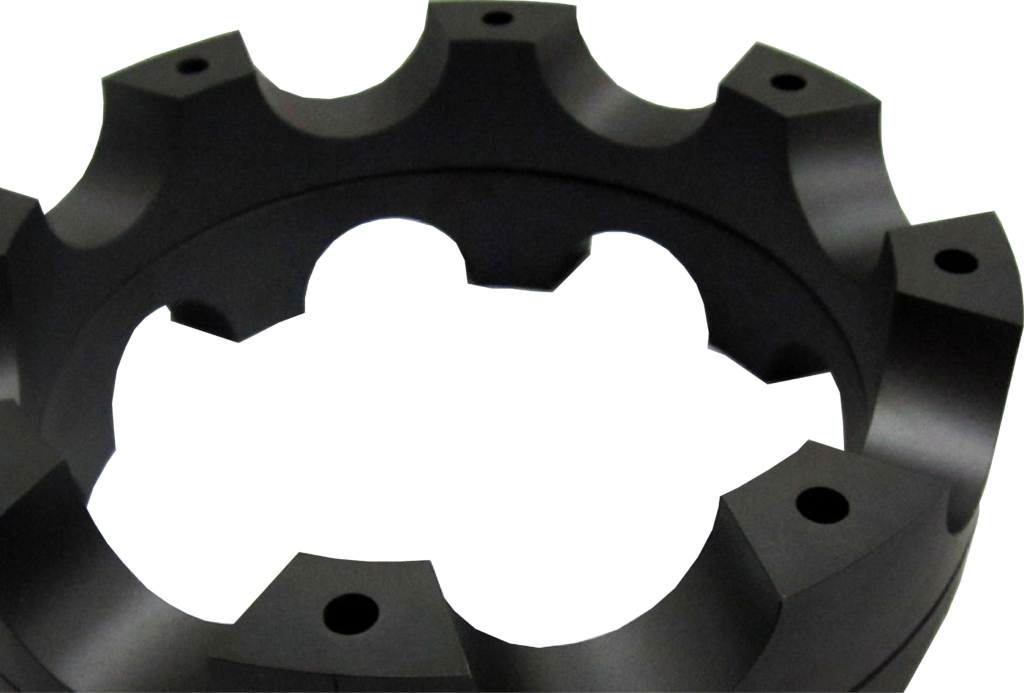
Exhibiting superior strength of stiffness, PAI offers creep resistance and an exceptionally low coefficient of linear expansion.
- Withstands Very High Temperatures
- Resistant to Aggressive Chemicals
- Superior Strength in High Temperatures
- Easy to Process
Contact us today to learn more about high-performance or imidized thermoplastic materials from The Gund Company, or request a quote for your application!
ENGINEERED THERMOPLASTICS
ALTHOUGH THEY SHARE MANY SIMILARITIES WITH COMMODITY THERMOPLASTICS, ENGINEERED THERMOPLASTICS ARE USED IN APPLICATIONS WITH REQUIREMENTS THAT EXCEED THE CAPABILITY OF COMMODITY THERMOPLASTICS.

Variations in characteristics between these materials do exist, but in general, engineered thermoplastics are used in environments where higher mechanical strength or elevated temperature resistance is required. In many cases, these environments exceed the capability of commodity thermoplastics.
COMMON APPLICATIONS USING ENGINEERED THERMOPLASTICS
- Automotive
- Medical & Healthcare
- Textiles
- Electronics
- Cookware
- Bearings & Springs
- Valves

Highly transparent, Polycarbonate offers good optical properties while offering superior mechanical stability at higher temperatures.
- Heat Resistant
- UV Resistant
- Impact resistant
- Electrically Insulating
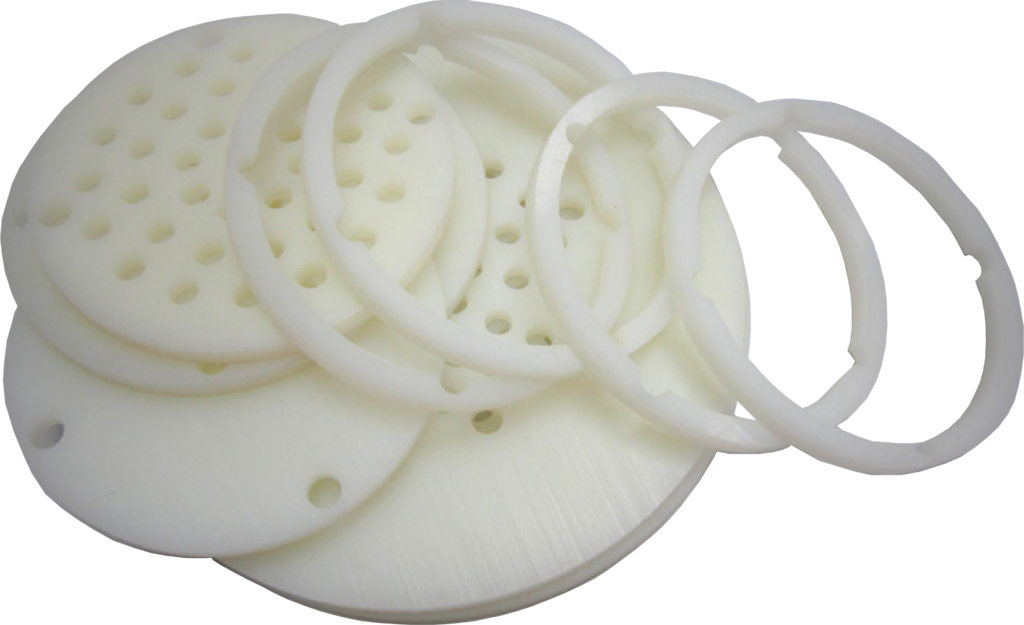
A polyethylene material like HDPE and LDPE, UHMW is chemically resistant offering superior mechanical and wear properties at high temperatures.
- Chemically Resistant
- Low Coefficient of Friction
- Extremely tough
- Superior Impact Strength
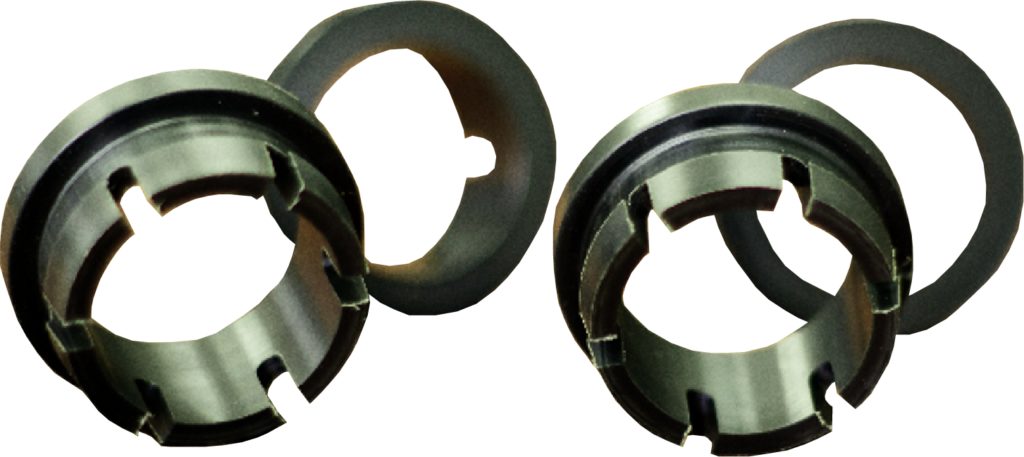
Acetal exhibits high strength and stiffness. It can be machined to tight tolerances and offers low moisture absorption, making acetal a common alternative to metals.
- Excellent Wear Properties
- Tight Tolerance Machining
- Low Coefficient of Friction
- Moisture Resistant
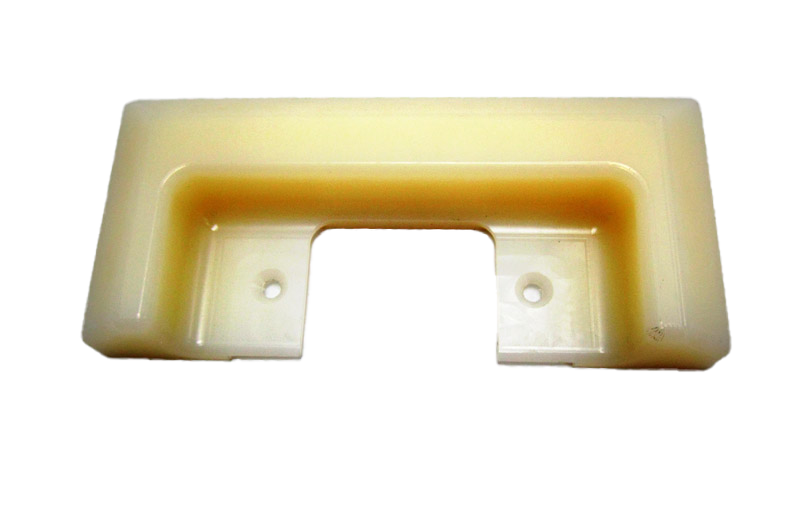
Nylon exhibits high strength and durability. It is lightweight, chemically resistant, and exhibits quick-drying properties making it ideal for outdoor applications.
- Chemically Resistant
- Quick Drying
- Lightweight
- Abrasion Resistant
Contact us today to learn more about engineered thermoplastic materials from The Gund Company, or request a quote for your application!
Check out our in-depth guide on selecting the right thermoplastic for your application!
COMMODITY THERMOPLASTICS:
COMMODITY THERMOPLASTICS – SUCH AS PP, PE, PVC, PS, AND PET POLYMERS – ARE COST-EFFECTIVE MATERIAL OPTION FOR ENVIRONMENTS WHERE EXCEPTIONAL PROPERTIES ARE NOT NECESSARY.

Applications using commodity thermoplastics do not require engineered or high-performance properties and do not require high heat resistance. Although there is some variability between these materials, commodity thermoplastics are by far the most common plastic used worldwide.
COMMON APPLICATIONS USING COMMODITY THERMOPLASTICS
- Textiles
- Automotive
- Toys
- Housewares
- Packaging
- Containers
- Electronics
- Construction
- Medical Applications
ABS
Korad®
Cycolac®
Absylux®
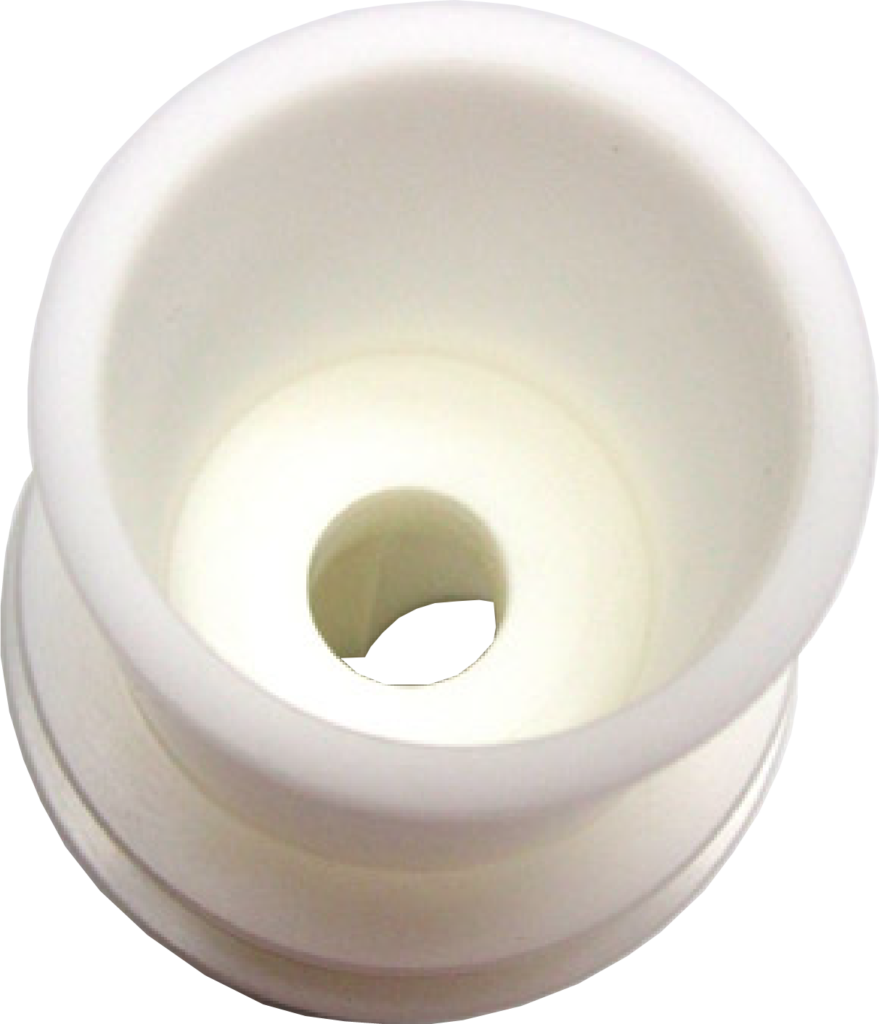
An FDA-compliant material that offers high strength, chemical resistance, and toughness compared to other commodity thermoplastics.
- Easy to Process
- Good Adhesion Properties
- Electrically Insulating
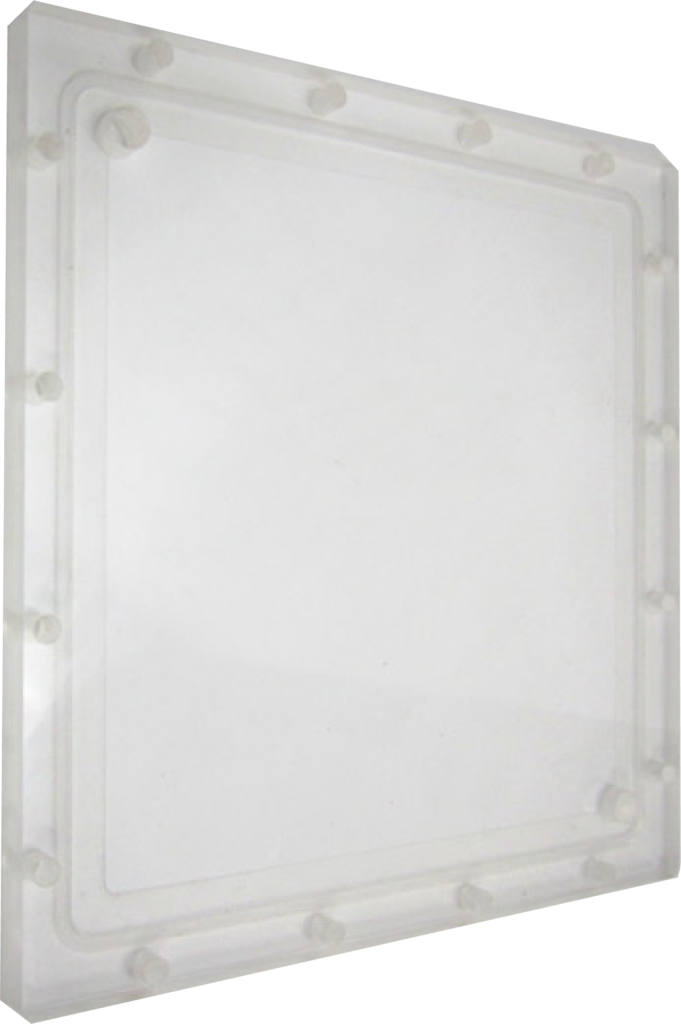
Acrylic exhibits good optical properties, UV stability, and impact strength at a lower cost when compared to alternatives in similar applications.
- Shatterproof
- Scratch-resistant
- Highly-transparent
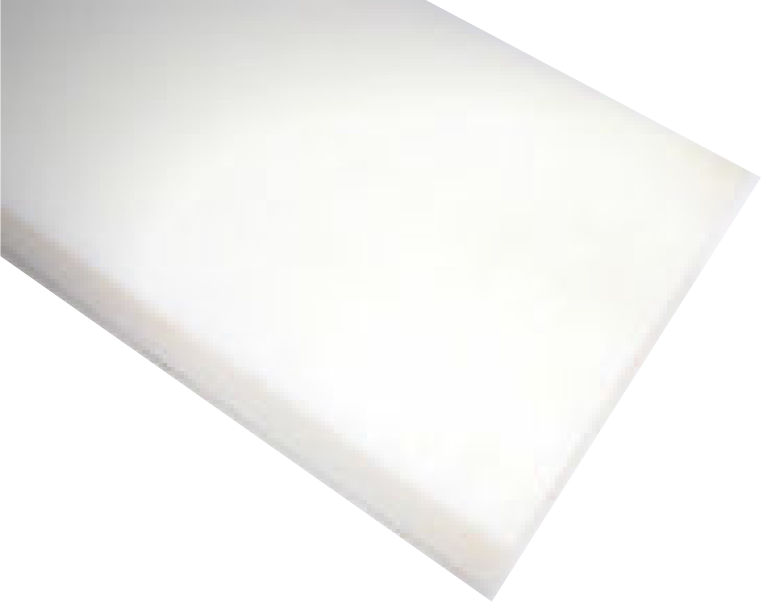
HDPE is a lightweight, chemically and corrosion-resistant thermoplastic with low-moisture absorption. HDPE is great in prosthetic and liquid storage applications.
- High Machinability
- Recyclable
- Chemically Resistant
- Low Moisture Absorption
PVC-CPVC
Kydex®
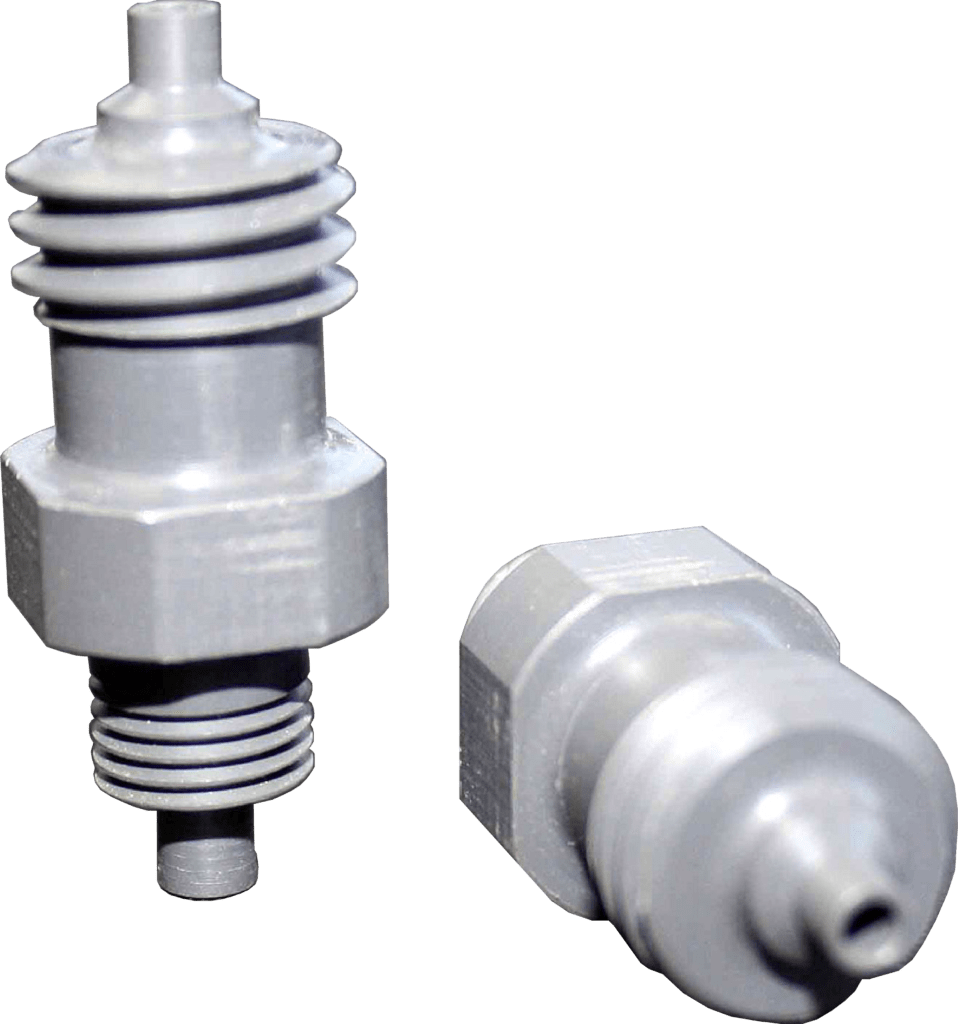
Flame-retardant and weather-resistant, PVC is a lightweight and durable thermoplastic used in plumbing, wiring, and medical applications.
- High Toughness
- Recyclable
- Electrically Insulating
- High Durability
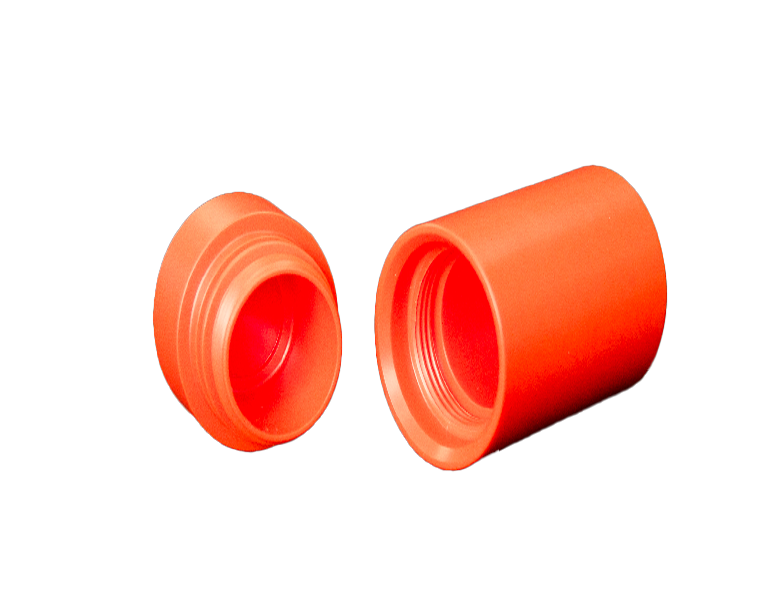
Polypropylene is an electrically insulating thermoplastic that offers superior flexural strength, and high moisture resistance.
- Electrically Insulating
- High Flexural Strength
- Chemically Resistant
- Pressure and Heat Resistant
Contact us today to learn more about commodity thermoplastic materials from The Gund Company, or request a quote for your application!
Versatile Thermoplastics: Manufacturing Methods, Applications, and Material Types
Thermoplastic materials can be homogenous and heterogeneous in their makeup. Unique properties can be achieved by blending thermoplastics, co-extruding thermoplastics, or even including special property-enhancing additives.
Check out our in-depth guide on selecting the right thermoplastic for your application!
Thermoplastics can be manufactured and fabricated using several standard methods. Most thermoplastic sheets and films are produced using an extrusion process. However, casting methods can also produce some sheet thermoplastic materials, as well. Nearly any thermoplastic sheet material can be formed using thermoforming, vacuum forming, or cold forming methods. Not only that, but thermoplastics with or without reinforcement can also be injection molded into complicated shapes, specifically with features that are not achievable through standard machining. All thermoplastic is often processed similarly. However, performance characteristics, workability, and cost can vary greatly.
Thermoplastic materials are suitable for numerous applications.
AMORPHOUS VS. SEMI-CRYSTALLINE THERMOPLASTICS:
Thermoplastics can be broken into two groups by composition: Amorphous and Semi-Crystalline.
While the molecules in semi-crystalline polymers are clustered and structured in a region, the molecules in amorphous polymers are randomly arranged.
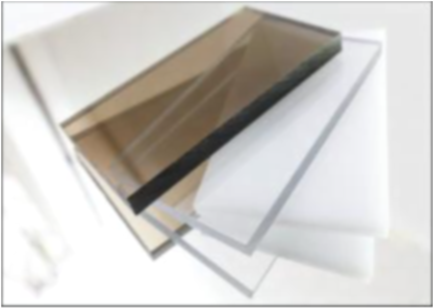
AMORPHOUS:
- Easy to thermoform
- Typically translucent
- Softens over a range of temperatures
- Bonds well using adhesives
- Good for structural applications
- Poor fatigue resistance
- Not ideal for wear applications
- Subject to cracking from stress
SEMI-CRYSTALLINE:
- Challenging to thermoform
- Typically opaque
- Sharp melting point
- Difficult to bond
- Good for structural applications
- Good fatigue resistance
- Good for wear & bearing applications
- Good resistance to cracking from stress
AMORPHOUS THERMOPLASTICS:
Amorphous thermoplastics are more conducive to thermoforming. They soften over a range of temperatures and have better bonding ability when combined with adhesives.
Amorphous plastics often have better dimensional stability and impact resistance, when compared to semi-crystalline thermoplastics of a similar grade. However, stress makes amorphous plastics more prone to fatigue and cracking.
SEMI-CRYSTALLINE THERMOPLASTICS:
Semi-crystalline thermoplastics are excellent for wear and structural applications.
Compared to amorphous thermoplastics, semi-crystalline thermoplastics tend to have better chemical resistance, electrical properties, and a lower coefficient of friction. However, semi-crystalline plastics are challenging to thermoform, difficult to bond, have a sharp melting point, and, additionally, have low impact strength.
Contact us today to learn more about thermoplastic materials from The Gund Company, or request a quote for your application!