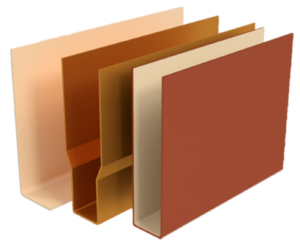
WHAT IS A SLOT LINER
A slot liner is a primary insulation component in a generator rotor, which provides an insulation barrier between the copper windings and the rotor forging.
The slot liner’s primary role in the rotor is to protect the winding from an electrical ground during operation.
It must also be strong enough to withstand the physical wear and tear of the assembly
process during winding. During operation, the slot liner will endure large centrifugal forces of generator start-up, steady state, and shutdown. Additionally, the slot liner will experience a wide temperature variation, from ambient conditions up to 130°C in operation, depending on the design.
Generator slot liners are typically made of a composite construction. The composite layup of different materials provides both electrical and mechanical properties to meet the specific demands of the application. The following selection guide will provide information on the different constructions available, the unique advantages and disadvantages of each, and tips for best practices in slot liner design in order to help engineers make more robust slot liner insulation specifications.
Slot Liner Construction
There are many materials that can be used to build a composite slot liner. The most common materials used are:
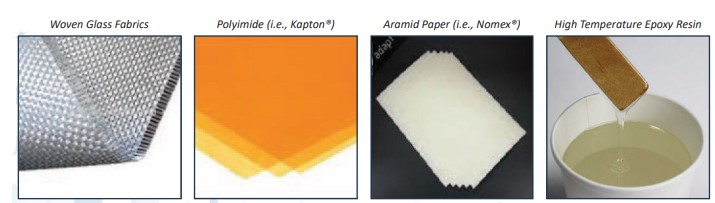
Each of these materials has specific electrical and mechanical properties that create a unique set of characteristics when combined during the slot liner composite fabrication. Epoxy has historically been used as the primary adhesive in slot liner composites due to its high-temperature electrical and mechanical properties. Woven glass fabric is often pre-impregnated with the epoxy resin and stabilized for further processing. This material is commonly known as glass-epoxy prepreg or b-stage. When heated and put under pressure, the epoxy prepreg resin will flow and bond the composite laminate layers.
Request access to view the entire selection guide.