Flexible Laminates
A Comparison of Properties and Costs
Motors use large amounts of flexible insulation. The following paper compares some of the most popular flexible insulation used for slot liners, phase insulation, coil wrapping, and other applications in motors. Each type of insulation provides varying levels of electrical and mechanical properties.
The first flexible insulations used in motors and generators were cellulose, other natural fiber papers, or felt materials. These insulations were used to fill the small gaps around the conductors, such as slot liner, conductor wrappers, and other areas where rigid insulations just could not be used.
The first flexible insulations used in motors were paper or felt materials for flexible insulations. These insulations were used to fill the small gaps around the conductors, such as slot liner, conductor wrappers, and other areas where rigid insulation just could not be used. The first laminates were produced using 2 or 3-ply laminations consisting of insulation paper, fleece, or film materials bonded together with a high-temperature adhesive. To improve their electrical and physical characteristics, materials continue to be added to laminates.
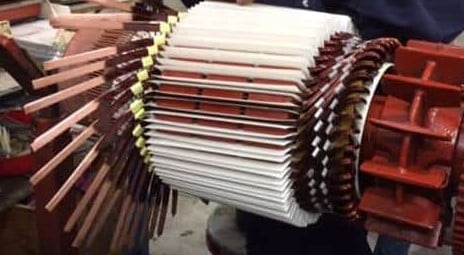
Common materials used in flexible laminates today include materials like:
• Rag Papers
• Polyester Fleece or Mats
• Polyester Films
• Aramid Papers
• Polyimide Films
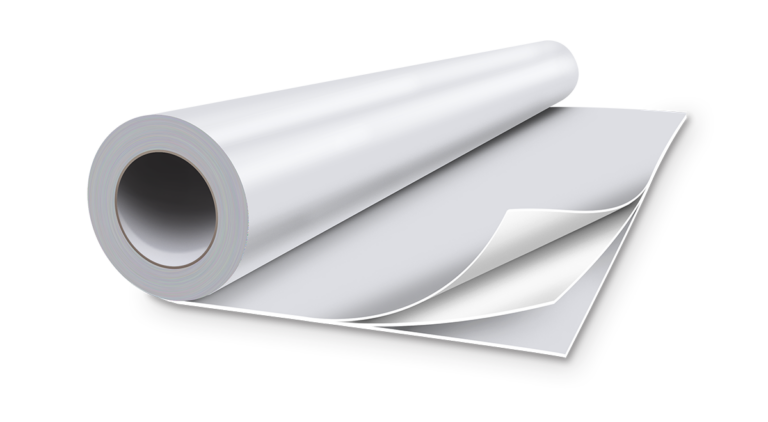
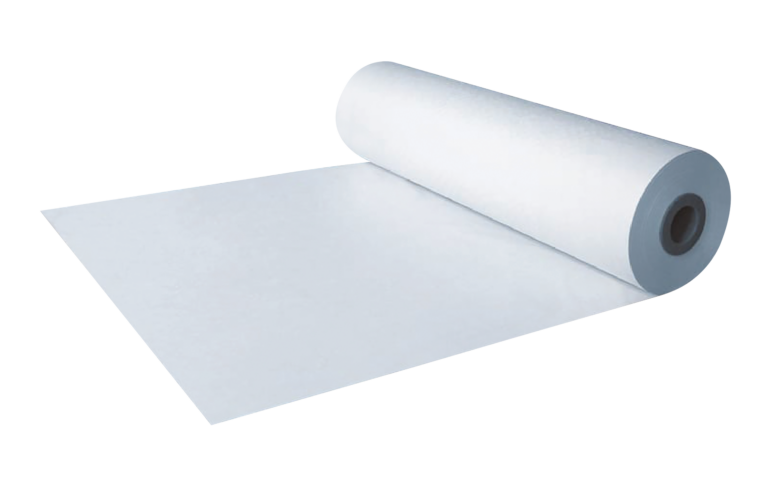
By combining these materials, the user has a list of material combinations or laminates for their selection. The combinations provide different temperature ratings, such as a Class F or H thermal class. They can provide extremely high dielectric strength, such as laminates used containing polyimide films. Each combination of materials also has a cost associated with it. The below table contains numerous electrical, thermal, and mechanical characteristics and a relative cost index for each material. Each laminate has varying price differences depending on the combination of materials and the thicknesses of each. Additionally, brand name products from the above lists can garner some high costs versus the more commonly known chemical names of the materials.
Product | Dielectric Strength | Tensile Strength | Tensile Strength | Tear Strength | Tear Strength | RTI (°C) | Cost |
Aramid (0.010″) | 6.4 | 26.2 | 14.2 | 6.1 | 3.7 | 210 | $$ |
DMD 70 | 9.5 | 80 | 60 | N/A | N/A | 155 | $ |
Aramid/Polyester/Aramid | 13 | 170 | 110 | 17 | 10 | 180 | $$ |
Aramid/Polyimide/Aramid | 13 | 170 | 120 | 12 | 10 | 220 | $$$$ |
| — | MD | XD | MD | XD | — | — |
For example, tradenames like Mylar® and Nomex® are trademarked names by the manufacturer for their brand of Polyester film (PET) and Aramid Paper. While these materials are excellent and are widely used, the scientific names have almost been lost due to the company’s marketing efforts. In addition, when manufacturers specify materials, they will forget to use the scientific or technical name of the material. Instead, they will use brand names. When these brand names are called out in a manufacturer specification, it is tough to be displaced primarily because people have again forgotten that these are brand names and not scientific names of the materials.
Click here to request access to this technical bulletin, plus everything in our Technical Resource Library!