The Significance of Arc Resistance in Material Selection
An electric arc occurs as a pure electrical discharge with a high current density. With the everyday use of power equipment such as circuit breakers or load-break switches, electric arcing results from electrical faults or short circuits. Due to increased current density, there is a temperature rise, resulting in additional heat generation. This heat causes the medium between the contacts to ionize (in the case of the air medium) or vaporize and ionize (in the oil medium). This ionized air or vapor acts as a conductor, and an arc is struck between the contacts.
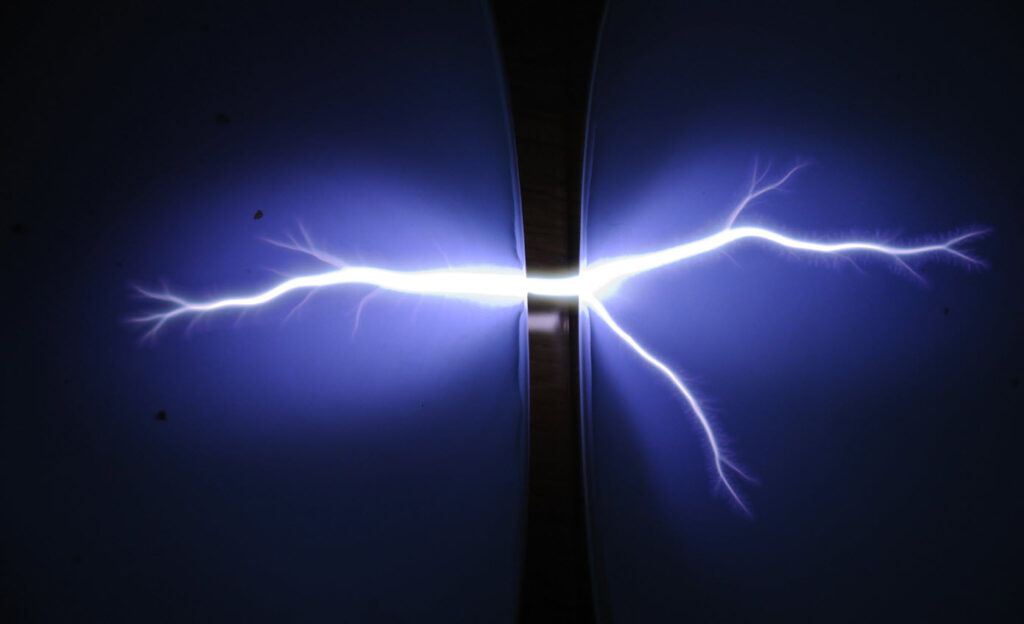
Arcing is inevitable when two conducting elements are brought together and sometimes leads to damage or failure of the electric system’s components and physical hazards. As a result, appropriate insulating or dielectric materials must be incorporated into the insulation system to control and handle high-voltage equipment.
Arc resistance is defined as insulating material to withstand a high-voltage electric arc and resist the formation of a conducting path along its surface. This conducting path results from thermal and chemical decomposition and material erosion. Therefore plastic materials with superior arc resistance properties are selected to handle applications susceptible to electric arcing. Tracking, which is commonly associated with arcing, happens when a high voltage current source leads to a leakage or fault path across the surface of an insulating material, slowly forming a carbonized way, which appears as a thin line between two electrodes. Tracking is accelerated by surface contaminants such as dirt, oil, or moisture. Since arc resistance varies from material to material, material property comparisons quantify the property in time units. It is expressed as the number of seconds a material resists the formation of an electrically conducting path along its surface when subjected to a high voltage, low current arc close to its surface. Thus, it is a natural source of differentiation between various plastic materials concerning arc resistance.
Failure of Plastic Materials Due to Electric Arc
The failure of plastic materials due to arcing happens by the following:
- Many inorganic, dielectric materials become incandescent when subjected to high-voltage electric arcs. Subsequently, they become capable of conducting electric currents. Upon cooling, they regain their insulating properties.
- Few organic compounds burst into flame without forming a visible conducting path across the material.
- Other materials fail as a result of tracking.
- The final form of failure occurs through the surface’s carbonization once there is enough carbon to conduct the electric current across the material.
Degree of ionization: The arc resistance increases with the decrease in the number of ionized particles between the contacts.
Length of the Arc: The arc resistance increases with the size of the arc. i.e., the length of separation between the contacts.
Cross-section of the Arc: The arc resistance increases with the decrease in the area of the arc’s cross-section.
Factors Affecting Arc Resistance Selection of Electric Insulating Material Based on Arc Resistance
Electric insulating materials are typically selected based on their resistance to Arcing or Tracking. Plastic materials, such as phenolics, tend to carbonize easily and have relatively poor arc resistance. However, plastics such as alkyds, melamines, and fluorocarbons have excellent arc resistance properties. Failures due to arcing do not always occur due to carbonization or tracking. Many plastics, such as acrylics, form ignitable gases that lead to product line failure instead of carbonization.
Arc Resistance of Plastics can be improved by adding fillers such as glass, mineral, wood, flour, asbestos, and other inorganic fillers. The table below shows the arc resistance of some common plastic materials.
Arc Resistance of Common Plastic Materials | |
---|---|
Materials | Arc Resistance (seconds) |
APO1 | 180 |
NEMA FR4 | 140 |
NEMA G-10 | 130 |
NEMA G-11 | 130 |
NEMA G-7 | 200 |
NEMA GPO-3 | 193 |
NEMA GPO-1 (Grade N155) | 150 |
NEMA GPO-1 (Grade N180) | 180 |
NEMA GPO-1 (Grade N220) | 180 |
U205 | 180 |
Ceramics may be used in severe applications with a significant risk of electrical damage due to arcing. Generally speaking, ceramics have better arc resistance compared to organic materials, such as plastics.
Arc Resistance Testing
To test various materials for their arc resistance, a standard method using a high-voltage, low-current set-up under dry conditions is available as per ASTM D495. Generally, this method is not used to conclude the relative arc resistance ranking of materials subjected to other arcs, such as low-voltage arcs at low or high currents. Due to its convenience and short testing time, the dry arc resistance test is intended for three reasons:
- Preliminary screening of materials
- Detecting the effect of changes in formulation
- Quality control testing** After correlation has been established with other types of simulated service arc tests and experience.
The test is usually conducted under clean, dry laboratory conditions, rarely encountered in service. Therefore, predicting the relative performance in typical applications and in varying clean to dirty environments may be substantially altered. There are also standards for testing arc resistance in wet and dry conditions if needed.
Conclusions
Electric arcing presents a difficult challenge and can negatively affect electric power transmission, distribution systems, and various electronic equipment. Arc resistance of different materials is represented as the total time they can retain their insulating properties without breaking down and causing current flow across their surface.
The arc resistance values may be used to evaluate the resistance properties of various plastics. Based on this, selecting the best material may be made, thereby reducing the risk of equipment damage, fire accidents, and human hazards.