The Gund Company | Success Stories
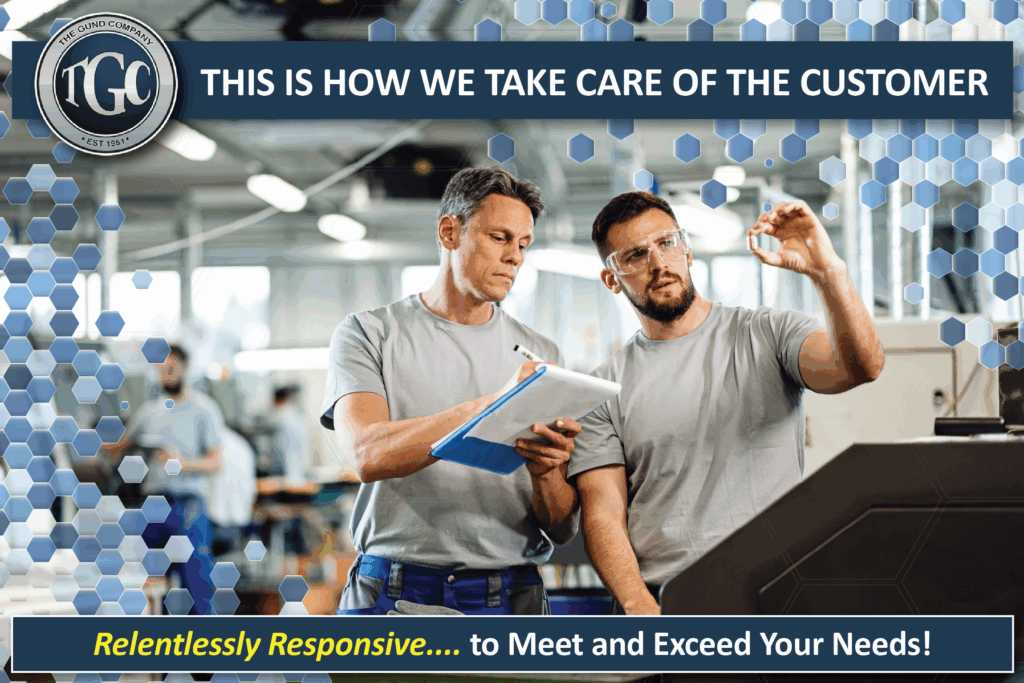
Delivering Under Pressure in Dallas
Two of our dedicated teams rose to the occasion a few weeks ago. Faced with an urgent request for long-time materials and parts needed for a critical customer witness test, they met the challenge and exceeded expectations.
With just two weeks to deliver, the team quickly brainstormed solutions and implemented a strategic action plan. This included identifying alternative materials that required customer approval. Thanks to the swift coordination and collaboration across departments, the deviation was approved in under 24 hours—an impressive feat that speaks volumes about the team’s agility and responsiveness.
One team had one of the required materials in stock, while the other sourced the remaining parts. Overnight shipping ensured the materials arrived at the customer’s facility in time to complete the necessary kits and assemblies. The final components were delivered the next day, fulfilling the customer’s critical purchase orders ahead of schedule.
Special recognition goes to everyone involved in this effort, from those who sourced and assembled the parts to those who handled logistics and communication. Your dedication, speed, and teamwork made a real difference.
This accomplishment is a shining example of what we can achieve when we work together with purpose and urgency. Thank you all for your outstanding contributions!

We are thrilled to celebrate the relentlessly responsive team at our Cedar Lake facility (CDL) for their outstanding work for a strategic customer.
On a recent Friday, we received an urgent call from one of our key contacts. They needed parts for a generator they were wrapping up at their plant. The team quickly reviewed the drawing, responded with questions and a quote, and maintained communication to finalize the order and address changes. As the window to complete the project on Friday slipped, we prepared for production and lined up the team to work over the weekend.
On Saturday, we received the purchase order and arranged for courier pick-up. The team adjusted the production plan and communicated effectively to complete the parts and prepare them for pick-up. By Monday morning, we received a thank you email from the customer, acknowledging the successful completion of the project. The team’s responsiveness and dedication ensured the customer’s needs were met, leading to potential opportunities.
In a remarkable display of dedication and teamwork, the Dallas team recently went above and beyond to ensure customer satisfaction.
On a recent Saturday morning, a multinational power management customer urgently requested the shipment of 1,000 pieces of a critical component for their assembly to prevent their production line from halting within three hours. Despite the challenge, TGC Dallas swiftly mobilized a crew to complete and package the parts for same-day shipping. Although the team initially had no one scheduled for Saturday work and no parts on the shelf, they prepared 300 parts and shipped them out for next-day delivery.
Special recognition goes out to the Dallas team for their extraordinary efforts. One team member expertly formed the parts, while another sacrificed personal time from a family event to ensure the parts were packaged and delivered to the carrier’s next-day delivery office.
Executive VP of Operations, Nels Ostrom, commended the Dallas team for their commitment to excellence and customer care. “Their actions prevented a significant disruption for a valued customer. By demonstrating such responsiveness and dedication, the team has reinforced trust and reliability, ensuring our customers can count on them in critical situations.”
The Gund Company received an urgent call from a nuclear power facility facing a critical failure of a generator current transformer (GCT). This posed a significant risk to the facility’s operations and required immediate attention to prevent downtime.
Understanding the gravity of the situation, our customer urgently requested specialized critical components. Our Milwaukee and St. Louis teams sprang into action, leveraging their expertise and resources to meet the demand. The seamless coordination between the two facilities showcased our ability to respond swiftly and efficiently to critical needs. Our employees’ dedication and hard work ensured that the required components were manufactured and delivered in record time.
Praises and Gratitude
The successful delivery of the components resolved the immediate crisis and exceeded the customer’s expectations. Our ability to overperform made our customers look like rockstars in the eyes of their stakeholders.
The mounting board of N220, with a GPO3 ring, worked perfectly in the current transformer, so our customer could deliver the safety-critical item to the nuclear power plant and avoid any further issues or downtime.
The customers were deeply appreciative of our swift response and outstanding service. They shared the following message with the team: “Please convey to the entire GUND team how exceptional we think they are and let them know how thankful we are for all their support with this urgent order.” – Amy Buyer
This experience highlighted the incredible impact The Gund Company can have on its customers and the broader community. Our swift action and high-quality products played a crucial role in ensuring the continued operation of the nuclear facility, thereby contributing to the safety and well-being of the community.
In the spirit of celebration and gratitude, we would like to highlight the extraordinary efforts of our team at the St. Louis plant. Their unwavering dedication and willingness to go above and beyond to take care of our customers, even during a holiday weekend, truly exemplify The Gund Company’s values.
Our story begins on a Sunday evening at 6:48 p.m. when an email arrived from our valued customer, Eric from Wisconsin, who was repairing an electric motor. Eric urgently needed a specific type of thick G11 material. After a phone conversation with Eric, it became clear that we could not manufacture the parts in the required timeframe. However, Eric agreed to accept a piece of the material measuring 4.500″ x 8.125″ x 34″.
Our team’s swift response to this challenge was commendable. They immediately went to the shop, located the material, and printed the Bill of Lading (BOL). The courier was then arranged to pick up the material from our team member’s home. By around 9:00 p.m., the material was on its way to Wisconsin, an approximately seven-hour journey.
Thanks to the collective efforts of our dedicated team, the customer received the needed material within 12-14 hours of contacting The Gund Company. This incident serves as a testament to the commitment and teamwork of our employees! It’s invariably a pleasure when we WOW our customers for always overperforming!
On Friday, May 24th, we received a notification from a customer about a production line being down due to an inventory discrepancy on their side. Our LOS management team quickly devised a recovery plan to determine how soon we could ship them the necessary parts. Given the upcoming Memorial Day holiday, some of our production team members were already scheduled to be off for the day. Despite working with a shortened crew, the LOS production team could pull together and complete the necessary tasks. The parts were completed today. Due to the holiday week and the inability of FedEx to deliver the parts to them on time, Victor, our plant manager, jumped in and offered to personally deliver the parts to their doorstep, 200 miles away, the following morning.
This is a true example of Taking Care of the Customer. Thank you, Victor, and the rest of the LOS Team!!
In a remarkable display of quick thinking and teamwork, employees at our Albany facility came together in the early morning of May 21st to assist a colleague in distress. At approximately 9 a.m., Jeremy Berger noticed that his co-worker, Jack, appeared in poor health while conducting a quality control inspection in the shipping area.
Jack’s condition, characterized by facial drooping and difficulty standing, prompted Jeremy to immediately offer support and escort Jack to the safety office. Greg Radnai, another employee, was quickly called to assess the situation and, without hesitation, transported Rob to the emergency room.
Jeremy and Greg’s prompt actions were pivotal in ensuring Jack received the urgent medical care he needed. Their decisive response was not only commendable but also potentially life-saving, as it may have prevented a more severe outcome. This incident serves as a powerful reminder of the importance of quick thinking and teamwork in emergency situations.
In the aftermath, the community spirit within the company was evident. A team member contacted Rob’s wife while another employee spoke with the ER nurse to ensure Jack was not alone. Discovering that Jack’s wife lacked transportation, arrangements were made for her to receive a vehicle from the plant to join her husband at the hospital. Greg further demonstrated his commitment by retrieving Jack’s wife and facilitating her travel to the ER. These actions reflect the company’s commitment to its employees and their families in times of crisis.
This incident highlights the importance of workplace camaraderie and the impact it can have during emergencies. The company’s staff showed commendable solidarity, proving that in times of need, colleagues can truly become lifelines.