How Does Moisture Impact Equipment Failure?
The effect of water absorption and moisture on electrical insulation properties is particularly interesting in the transformer, switchgear, electronic, motor, and generator industries. It is being studied at universities and by active working groups under the auspice of many technical and standard associations such IEEE (Institute of Electrical and Electronics Engineers). The Gund Company actively participates in such activities and is willing to share the latest knowledge and advances on this subject with customers…
Chemistry of Water Molecules and Interaction with Solid Electrical Insulations
Water in the form of condensed water vapor (moisture) on the surface of solid insulation attracts airborne dust. It allows for the dissolution of corrosive gaseous contaminants, which promote the ionization of water. The presence of a significant amount of ionized water molecules reduces surface resistivity and shortens creepage distance.
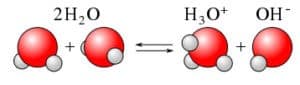
Also, the dipole nature of a water molecule promotes polarization (dielectric dissipative loss) and reduces dielectric withstand… if entrapped in a significant amount.
Moisture can accumulate on solid insulation in four different ways. A, B, and C can be progressive in nature.
- A. Free moisture – condensation on the surface of the solid insulation in high ambient humidity, especially from repeated thermal cycling.
- B. Absorbed moisture through dipole attractions on solid insulation with polar functional groups.
- C. Combined moisture as a result of hydration between moisture and insulation through prolonged exposure, resulting in the formation of -OH hydroxyl groups.
- D. Lastly, certain solid insulation releases moisture during thermal degradation, advanced aging, or post-curing/polymerization.
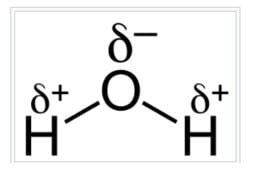
Besides ambient condition, water absorption and moisture content (hygroscopicity) of solid insulation is also influenced by the chemistry (polarity) of the resin and substrates/fillers in the case of composite materials.
Natural (plant) based materials are more hygroscopic than natural inorganic compounds like calcium carbonates, clays, talc, etc. Synthetic materials are usually less hygroscopic.
Amongst synthetic organic materials, those with more polar, or complicated, functional groups like O-H, C-halogen, imide, and amide have a higher tendency to absorb moisture than those with C-C, C-0, and C-H groups.
Fibrous structure absorbs and retains moisture more readily than highly cross-linked structures because of the presence of more active sites… Thin-film material absorbs and retains more as the surface area exposed per unit volume is higher.
The table below shows typical water absorption or moisture contents of solids commonly used in electrical insulation. As discussed above, the moisture content is dependent on the ambient temperature and humidity so the table should be used for comparison between classes in a similar environment only. It is no surprise that vulcanized fiber is seldom used nowadays in a critical application and cellulose pressboard and paper are always used impregnated with dielectric insulation fluid after extensive dry-out. Polymeric materials or fiber-reinforced polymeric composites are used as stand-alone solid electrical insulation.
Water Absorption of Common Materials | |
---|---|
Materials | Water Absorption (%) |
Polyolefins, i.e., polypropylene, polyethylene | 0.01 to 0.05% |
Polycarbonate, polyester | 0.1 to 0.3% |
Glass Epoxy and Glass Polyester Composites | 0.1 to 0.5% |
Glass Phenolic and Melamine Composites | 0.5 to 1% |
Inorganic insulation like treated Mica, silicate glass microfiber | 0.5 to 1% |
Paper and Canvas Phenolic and Melamine Composites | 1 to 4% |
Synthetic Fibers like Kapton and Nomex | 2 to 10% |
Natural Cellulose-based materials – non impregnated | 2 to >30% |
Difference Between Moisture Content and Water Absorption Test Methods
There are several ASTM, IEC, and other standard methods to measure moisture content in solid electrical insulation. They can be grouped into two types.
Type I: Moisture Content Determination by Karl Fisher Titration
- IEC60814 – Determination of water in insulating liquids and oil-impregnated cellulosic insulation.
- ASTM D3277-95 – Standard test methods for moisture content of oil-impregnated cellulosic insulation.
- ASTM D1348-94C – Standard test methods for moisture in cellulose.
Type II: Moisture Content Determination by Weight Loss Method (i.e., balance method)
- ASTM D1348-94A/B – Standard test methods for moisture in cellulose.
- ASTM D6980-04 – Test method for determination of moisture in plastics by loss in weight.
- ISO 287 – Paper and Board, Determination of moisture content – oven drying method.
- TAPPI – T412 Moisture in Pulp, Paper, and Paperboard, test methods.
All but one of the above Moisture Content Test Methods are developed for the plant (i.e., cellulose) based insulation with a relatively high level of moisture in natural equilibrium. The samples are tested “as found” as any pre-conditioning would bias the moisture level in the natural state. Accuracy and precision often suffer due to difficulties in maintaining “as found” moisture levels in sample preparation and handling and from interference from substances other than water that is volatile at lower than 110 °C or degrades above 100 °C. This is especially the case with materials with a lower moisture content level.
Test for Water Absorption
For polymeric materials and composites where the level of moisture in natural equilibrium is usually much lower, measuring its ability and tendency to absorb moisture is often a more precise and practical approach.
ASTM D570-08 Water Absorption of Plastics
This is a “weight gained” instead of a “weight loss” method where the pre-conditioning at elevated temperature dries out and stabilizes the sample. This provides a more consistent baseline for determining weight gain from water immersion. The test can be done for a 24-hour duration or longer term to achieve constant final weight gain.
Conclusion
Water absorption data could provide additional insights into the short-term and long-term performances of insulation in real-life environments. It relates directly to the chemical and hygroscopic nature of the insulation and its constituents. It allows the end product designer to select and optimize the type of insulation best suited for an environment where humidity is the main concern and to design countermeasures. It can also be used for material quality and process control purposes, i.e., dry glass and unsaturated sites in the polymer chains.