Water Absorption on Electrical Insulation
The Gund Company fabricates custom electrical insulating components for power systems equipment, including generators, transformers, switchgear, power supplies, electric motors, induction furnaces, electric arc furnaces (EAF), and related equipment.
Insulation material selection can be quite a challenge due to the factors influencing insulation system engineering and insulation component design.
Moisture, especially when combined with aggressive gases and dust, causes atmospheric corrosion. This corrosion can fail circuit breakers, bus bars, relays, integrated circuit boards, and transformers. The greatest danger lurks in conditions where electronic equipment is exposed to relatively high air humidity or extreme variations in temperature, such as day-and-night operation or outdoor installation. Failure of components in such cases is usually caused by changing contact resistances, flashovers, creepage currents, corona, or reduced insulation properties.
The moisture absorption of a material is a critical property that is often overlooked. According to ASTM D570, the American
Standard Test Method for Determining the Water Absorption of Plastics, “the moisture content of plastic is very intimately related to such properties as electrical insulation resistance, dielectric losses, mechanical strength, appearance, and dimensions.” Of course, with insulation materials, the absorption of water from high humidity conditions can result in the original design insulator becoming a conductor.
The chart below shows the water absorption properties of several common rigid insulation materials used in electrical and electronic equipment applications. Note that the values below are the maximum allowable water absorption percentages per the NEMA Standards for laminate insulation materials.
To read the full article and gain access to our other technical white papers, click here!
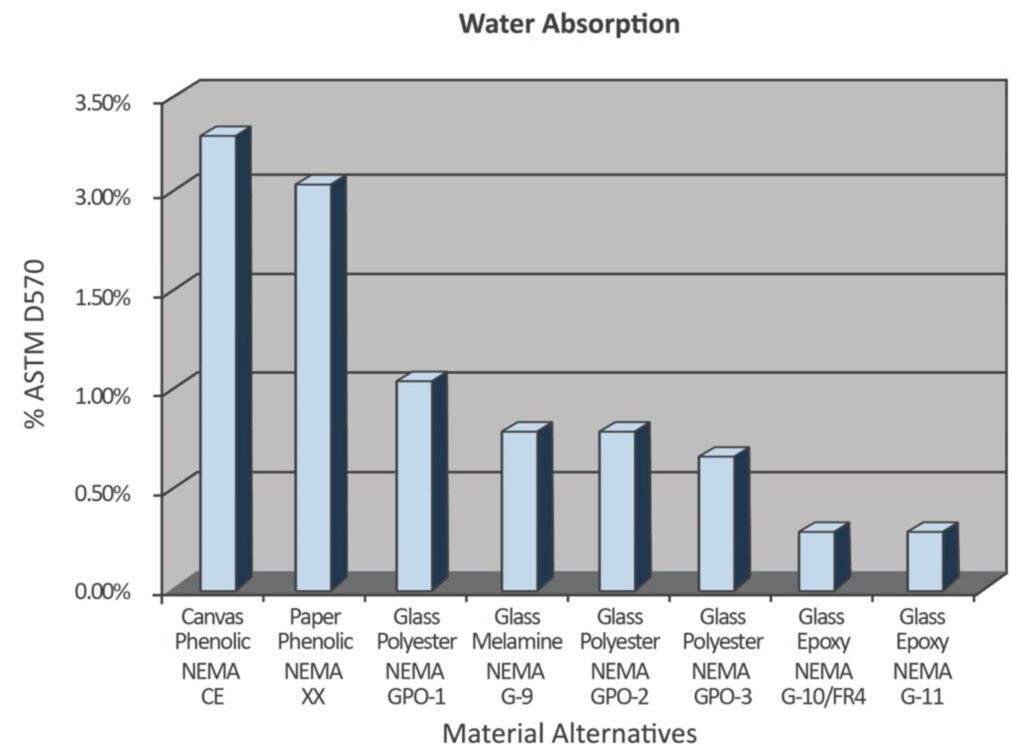